What does one of the most capable all-terrain vehicles in the world, yet at the same time one of the most practical for everyday use, have to do with documenting welding data? The huge ground clearance and built-in deep wading capabilities of the Mercedes G drop a clear hint: The vehicle is designed to cope with the most extreme off-road conditions – pulling force and a long service life have to be guaranteed when the G is subjected to violent impacts at high speeds on rough terrain, which also exerts continuous loading on all the welds. This is why quality assurance and optimization of the production processes using a sophisticated welding data management system are so vital.
Production of the Mercedes G frame at Magna Presstec
The stringent quality requirements placed on the G class – demanded by manufacturers and end users alike – are reflected in the ever-increasing demand for the premium offroader. To be able to produce the vehicle in the desired quantities, a high degree of automation is essential in the production of the chassis frame.
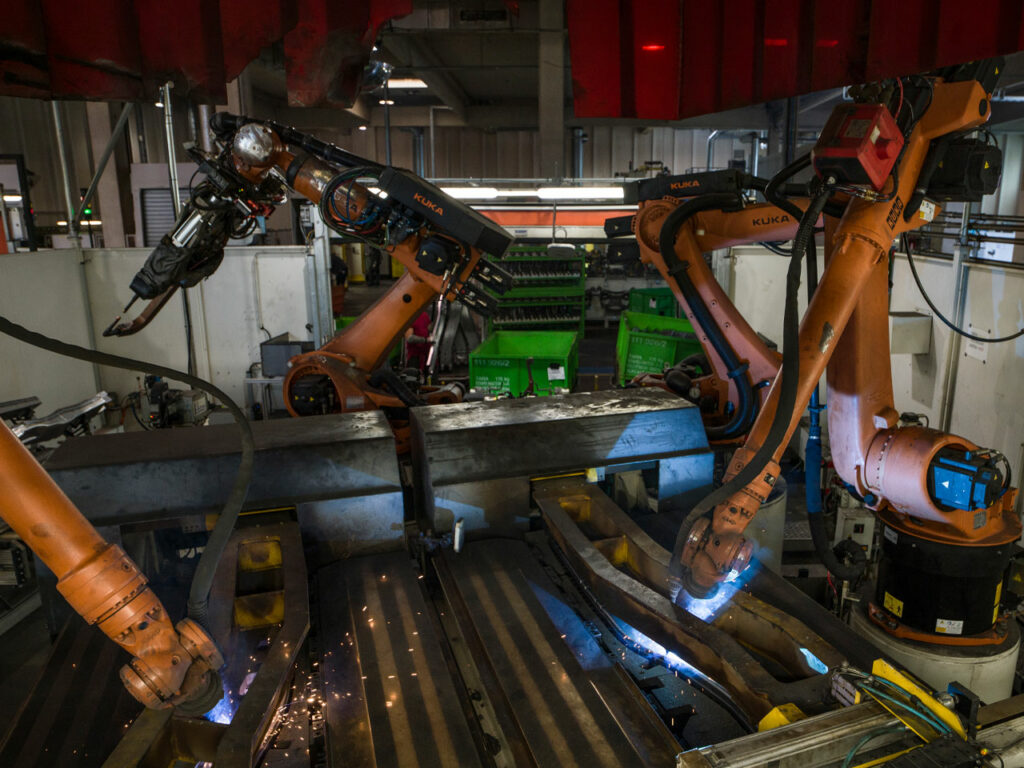
The high-tech production line of Tier 1 supplier Magna Presstec in Lebring in southern Austria has the lot: Robotic welding and handling systems merge together perfectly along the 100-meter line. An extremely fast, highly accurate, and digitally controlled pulse welding process (PMC from Fronius) meets all the stringent demands placed on the essential joining technology.
The production line is tooled up with the individual parts at the start of the line. A complete Mercedes G chassis frame – suspended as if by magic from an overhead crane – then leaves the manufacturing hall every 10 minutes.
Extremely complicated: autonomous peak production in detail
“Our mission is to make every frame identical to all the others. There mustn’t be any deviations,” stresses Kurt Hartmann, production manager and welding supervisor at Magna Presstec.
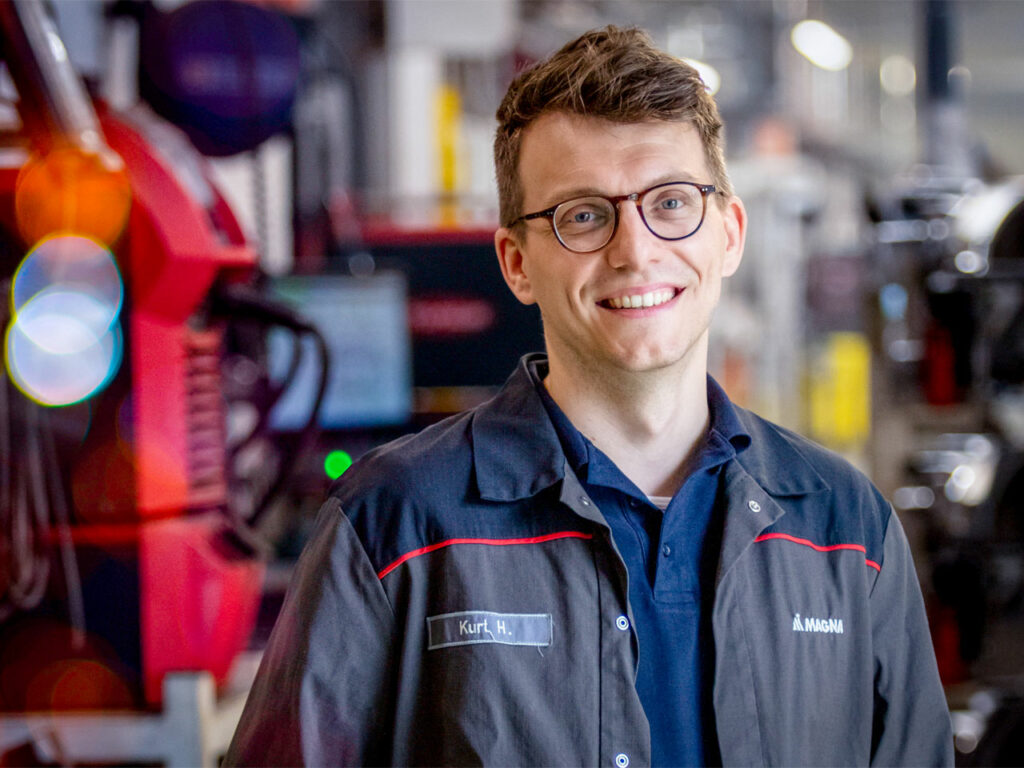
Front and rear of the frame: “We manufacture in three sections,” notes Hartmann, addressing the details. “The front and rear of the frame – in other words the first two sections on the production line – are produced at the same time. A team of workers starts by tooling up the welding units.
Then, in the cells, the components are joined using welding robots. A handling robot picks up the completed components, transports them to the next cell and places them in position. At the end of each section is a cell to which the workers have no access. This is used for welding long welds, but also for cooling or as a complex station for squeezing, for example, which involves nesting the lower shells with the upper shells of the side members, moving them into position and welding them under pressure.”
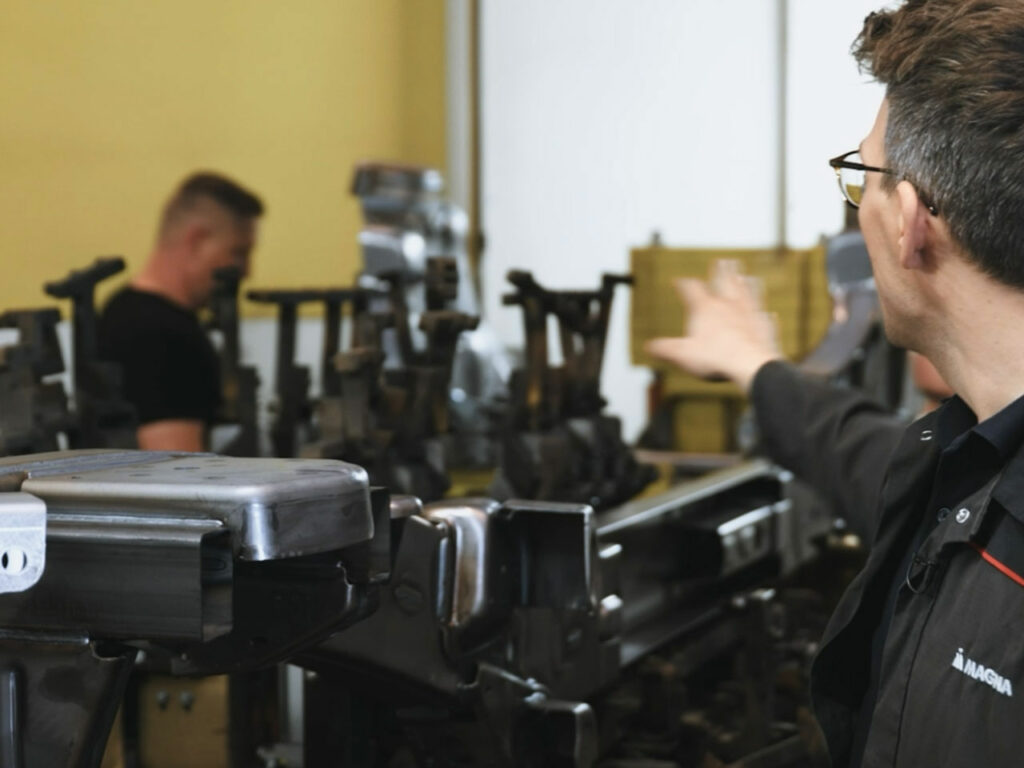
Substructure: “In the substructure – the final production section – the front end and rear end of the frame are coupled together and the frame takes on its striking form,” continues Hartmann. The final work steps consist of punching decoupled connecting points for the chassis. In addition, a drawn arc welding process fires 192 studs into the frame. A trained welding inspector then checks the quality of the welds, removes any remaining welding spatter, and reworks the welds as necessary.
Complete quality assurance also involves 100% measuring of the frame using robot-controlled laser measurement technology. Once the frame has undergone its final checks, it leaves the bodywork section on a Power&Free system (conveyor) and is passed on to the next stage in the manufacturing process.
Quality assurance: monitoring of welding data with WeldCube Premium
But having an outstanding welding process is not in itself sufficient for Magna Presstec to satisfy the demanding quality requirements of the G model. A system is needed to replace the missing “eyes” along the 100-meter production line – something that will provide 100% monitoring and comprehensive documentation of the welding process.
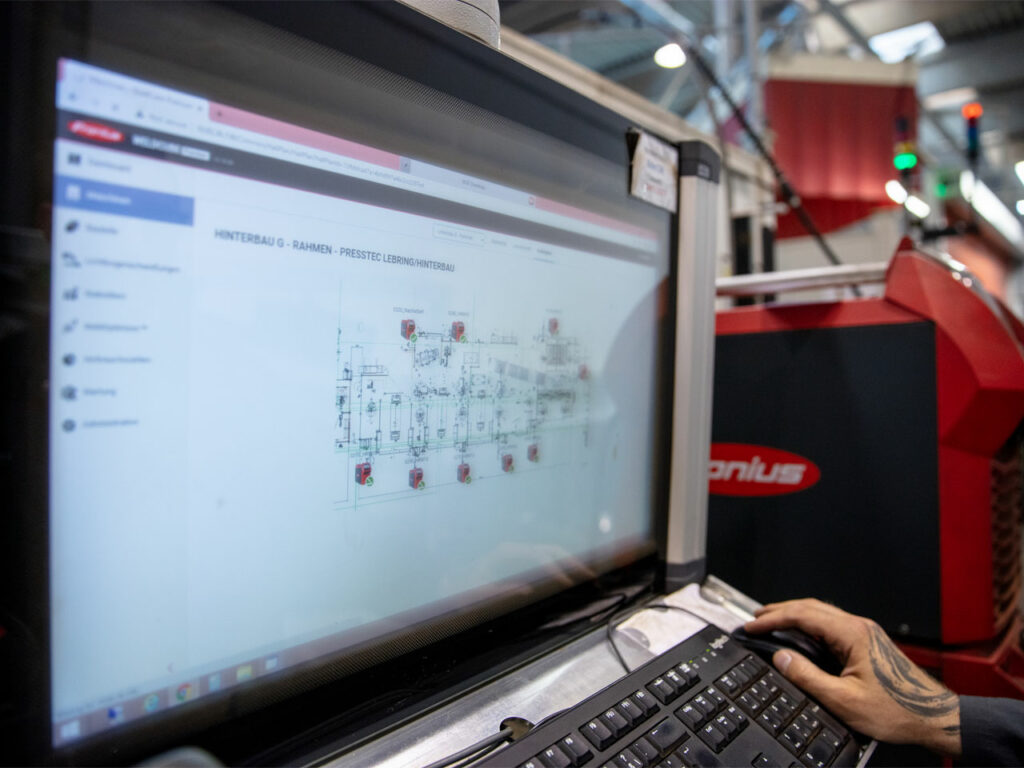
Hartmann is convinced. “WeldCube Premium is an important pillar of our quality management system. The complete traceability of every single weld is incredibly important to us. Trained operators at the quality control stations are presented with the most accurate information on their terminals: Are there any dubious or real faulty welds?
Using WeldCube, in other words using the welding data, enables potential error locations to be highlighted, subjected to a detailed visual inspection, and reworked if necessary. Only then is the G frame released to the next stage in the process.” The gathered data are then fed back to help optimize the automated welding processes.
From monitoring to predictive maintenance
“The fact that WeldCube Premium scrupulously charts every millimeter of the weld makes it a simple matter for us to use analysis tools to determine the cost of consumables such as gas and welding wire. Yet it has much more potential, for example predictive maintenance, or rather the ability to order wear parts and other materials in good time and in sufficient quantities,” is how Hartmann sees obvious perspectives for the future.
“Predictive maintenance with WeldCube Premium was able to uncover other areas of huge potential savings for us – for example, by having the welding management system specify precise maintenance intervals. We’re always kept fully informed about the condition of contact tips, torch bodies, welding torches, and wirefeeders, which means we know exactly when to service the equipment to avoid faulty welds, rework, or even the scrapping of components.“
For special jobs: specialists only!
But documenting and analyzing the welding data is not enough for Magna Presstec: “We’re already using the Central User Management (CENTRUM) software package, which also assists us in quality management. CENTRUM is where user and welding permissions are centrally managed. Welders use a chip card to identify themselves to the welding system, ensuring that specific tasks are only carried out at the right location by trained operators using the relevant welding parameters – another way of eliminating potential sources of error,” is Hartmann’s reassuring conclusion.
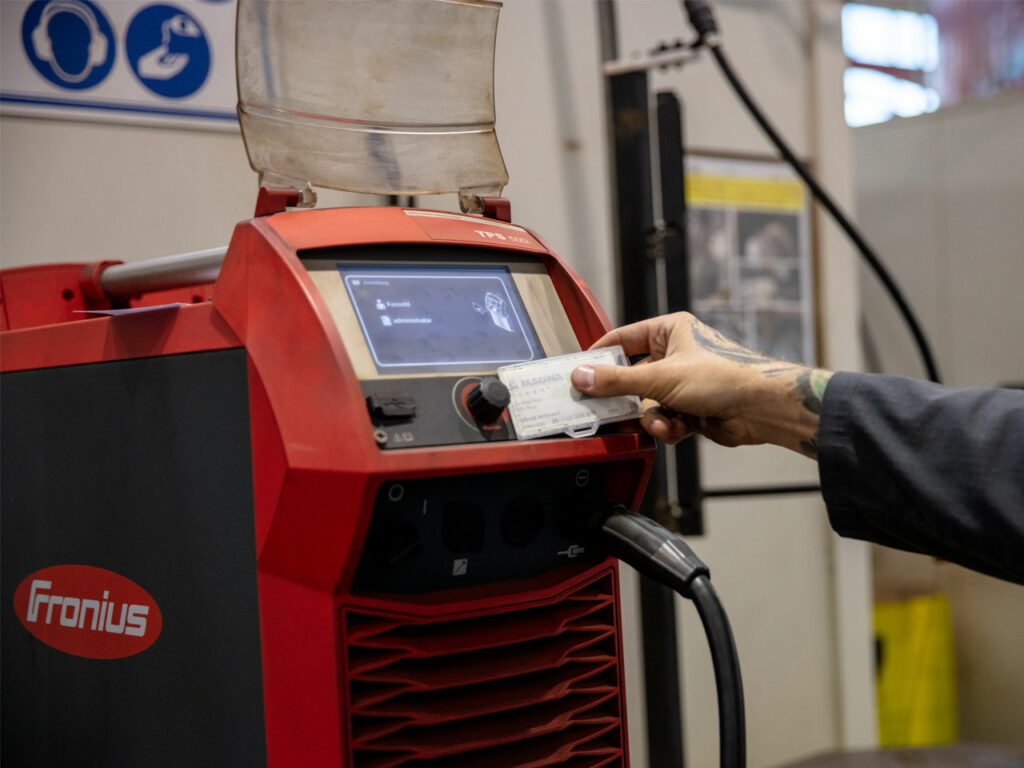
Fronius solutions for the documenting of welding data
All the software packages used by Magna Presstec were developed by Fronius. However, all the products, starting with WeldCube Premium right through to Central User Management, emerged following an intensive exchange of ideas with Magna Presstec: The extended testing of prototypes on Magna production lines allowed the necessary information to be obtained and the software to be fine-tuned ready for the market.
Take a quick look at our short video showing the production of the frame for the Mercedes G at Tier 1 supplier Magna Presstec:
If you are also interested in our future-oriented solutions supporting autonomous production, then click here for additional product information.
2 Comments
Jony
14. April 2023 at 16:23Hi dear,
I enjoyed reading the great blog about the process of documenting the welding on your vehicle.
Hope to get more in the future.
Suyash
17. April 2023 at 11:43thanks for sharing us!