Wir alle leben in einer eruptiven und volatilen Zeit. Energiewende, geopolitische Spannungen sowie unsichere Lieferketten stellen uns beinahe täglich auf die Probe. Die Diskussionen verlaufen oft kontrovers und hitzig. Eines ist aber fix: In der Produktion sind wir mehr denn je gefordert – weil sie in Zukunft ressourceneffizienter, schneller, flexibler, wirtschaftlicher, umweltschonender und in geringen Losgrößen erfolgen muss. Hier kommt Metall-3D-Druck ins Spiel.
Metall-3D-Druck: Was ist das eigentlich?
Der Metall-3D-Druck ist – so wie auch alle anderen 3D-Druck-Verfahren – ein Fertigungsverfahren, das die Erzeugung vieler Produkte sowohl technisch als auch ökonomisch revolutioniert hat. Schicht für Schicht wird heute real, was gestern noch unmöglich schien. Dabei werden dreidimensionale Objekte durch lagenweises additives Auftragen von Grundmaterial erzeugt. 3D-Druck nimmt mittlerweile in immer mehr Branchen erfolgreich Fahrt auf. Er erhöht die Flexibilität und damit die Konkurrenzfähigkeit vieler Betriebe in der Automobil-, Elektronik- und Konsumgüterindustrie, in der Öl- und Gasindustrie, Luft- und Raumfahrt, im Kraftwerksbau, im Werkzeugbau, in der Medizintechnik und im Baugewerbe.
Metall-3D-Druck bietet jede Menge Möglichkeiten und zahlreiche Vorteile
Klassische Fertigungstechniken erfordern oft einen aufwendigen Formen- und Werkzeugbau, gepaart mit langen Vorlaufzeiten und hohen Einrichtungskosten. Die additive Fertigung hilft, die Entwicklungszyklen immens zu verkürzen. Das Drucken von Bauteilen on demand beschleunigt den Prototypenbau (Rapid Prototyping), ermöglicht eine Just-in-time-Fertigung mit Verzicht auf Lagerhaltung von Ersatzteilen sowie -kosten und vereinfacht Reparaturarbeiten wesentlich.
Werden Ersatzteile benötigt, wählt man die richtigen „Rezepte“ in der Software und druckt bzw. kopiert sie nach Bedarf. Grenzen für Bauteilgeometrien gibt es kaum. Sogar komplizierte Waben- und Hohlraumkonstruktionen sind möglich. Einen besonderen Vorteil bietet der Metall-3D-Druck beim Prototypenbau: Designprobleme lassen sich frühzeitig erkennen und ohne aufwendigen und teuren Formen- und Vorrichtungsbau beheben. Gleichzeitig beschleunigt das Verfahren Innovationen und erhöht die Leistungsfähigkeit von Betrieben. Häufig sind gedruckte, form- und belastungsoptimierte (topologieoptimierte) Komponenten leichter als herkömmliche und reduzieren zum Beispiel den Treibstoffverbrauch von Autos oder Flugzeugen. Auch die Nutzlast von Transportfahrzeugen kann mit gedruckten, gewichtsoptimierten Bauteilen erhöht werden.
Metall-3D-Drucken mit Highend-Schweißtechnologie
Bei 3D-Druckverfahren können wir aus verschiedenen generativen Verfahren wählen. Dabei werden Gegenstände durch Verbinden einzelner Materialschichten lagenweise aufgebaut und in Form gebracht. Im Metall-3D-Druck unterscheiden zwischen pulver- und drahtbasierten Prozessen. Beim Pulververfahren wird Metallpulver aufgeschmolzen. Die gängigste Variante, das Pulverbettverfahren, besticht durch hohe Präzision, ist aber relativ langsam. Drahtbasierte Prozesse schmelzen den Draht ab und bauen so das Werkstück auf – entweder elektronenstrahl-, laser- oder lichtbogenbasiert. Sie verfügen über hohe Abschmelzleistungen und tragen so zu kurzen Fertigungszeiten bei.
Wire Arc Direct Energy Deposition, kurz DED-Arc, ist lichtbogenbasiert und nutzt den Metall-Schutzgas-Schweißprozess (MSG). Diese Metall-3D-Druckvariante ermöglicht uns Abschmelzraten von bis zu 4 kg/h, die zukünftig durch spezielle Prozesse und Mehrdrahtlösungen noch gesteigert werden. Anlagen- und Materialkosten sind wichtige Faktoren bei der Wahl des Druckverfahrens. Im Zentrum bei DED-Arc steht ein stabiles Schweißsystem. Teure Vakuumkammern, wie sie beim Elektronenstrahlverfahren zum Einsatz kommen, fallen weg. „Für ein gutes Druckergebnis ist vor allem der richtige Schweißpfad mit den passenden Schweißparametern und -prozessen entscheidend“, erklärt Philipp Roithinger, Experte für additive Fertigung. „Darüber hinaus benötigt man ein automatisiertes Schweißsystem, das die Pfadgenauigkeit des Schweißbrenners sicherstellt. Hochwertige Schweißroboter bieten heute eine Pfadgenauigkeit von bis zu 0,7 mm und eine Wiederholgenauigkeit von bis zu 0,06 mm.“
Bauteilfertigung im großvolumigen Metall-3D-Druck
Bei DED-Arc sind Stabilität und Temperaturmanagement des verwendeten Schweißprozesses essenziell. Dieser muss so energiearm, also so „kalt“ wie möglich, ausgeführt werden, damit nicht zu viel Energie ins Bauteil fließt. Außerdem soll die geschweißte Lage durchgängig, spritzerfrei und gleichmäßig sein. Käme es zu einem Schweißfehler, würde sich dieser in den darüberliegenden Lagen fortsetzen.
Der einzigartige MSG-Prozess Cold Metal Transfer (CMT) erfüllt mit seinen intelligenten Prozessregelvarianten bereits jetzt die hohen Ansprüche, die wir für die additive Fertigung an die Schweißtechnik stellen. „CMT zeichnet sich durch einen enorm stabilen Lichtbogen aus und ermöglicht einen flexiblen Wärmeeintrag“, erklärt Roithinger und ergänzt: „Der Prozess ermöglicht einen annähernd spritzerfreien Werkstoffübergang. Das hilft, Fehler zu vermeiden und die Nacharbeit zu verringern. Darüber hinaus können wir mit CMT hervorragende Abschmelzleistungen erzielen und die Tropfenablöse jedes einzelnen Tropfens steuern. Auf diese Weise können wir noch präziser arbeiten. Zudem haben wir den Prozess mit CMT Additive Pro noch weiter für die additive Fertigung optimiert, um einerseits einen konstanteren Lagenaufbau sicherzustellen und andererseits ein besseres Wärmemanagement zu ermöglichen.“
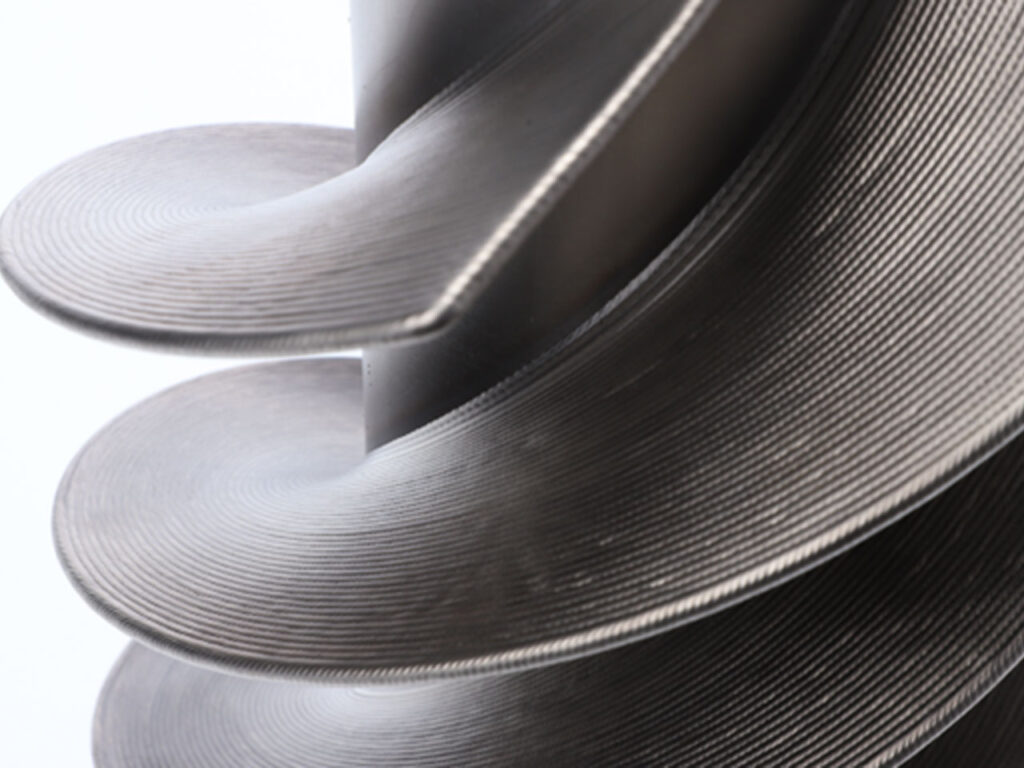
Beim Metall-3D-Druck den Lichtbogen stets im Blick
Trotz Hightech-Equipment ist es von Vorteil, wenn Schweißexpertinnen und -experten ein Auge auf den Lichtbogen samt Tropfenablöse haben. Mit speziellen Kamerasystemen lassen sich die Schweißarbeiten überwachen und potenzielle Fehler erkennen. Bei Bedarf kann rechtzeitig eingegriffen werden. ArcView 2 zum Beispiel ist eine prozessgetriggerte Kamera, die es erlaubt, den Prozess direkt vom Arbeitsplatz aus zu überwachen. Die Kamera liefert gestochen scharfe Bilder – im Millisekunden-Bereich! Die einzelnen Fotos entstehen in der Kurzschlussphase, also genau dann, wenn kein Lichtbogen vorhanden ist. Unzählige davon liefern den Schweißfachkräften ein perfektes Realtime-Video für die Prozesskontrolle. Dieses kann auf einer Bildschirmkonsole außerhalb der Roboterschweißzelle betrachtet werden. Auf diese Weise sind Schweißerinnen und Schweißer bestmöglich vor Lichtbogenstrahlung geschützt.
Ökonomisch und ökologisch interessant
Alternative Fertigungsmethoden zum additiven Fertigen wären Fräsen oder Zerspanen. Dabei entsteht jedoch jede Menge Abfall, da die benötigten Teile aus Metallblöcken – oft aus riesigen – herausgeschnitten werden. Hat man einen Hohlkörper, ist der Verschnitt enorm. Bei additiver Fertigung erzeugen wir das Bauteil Schicht für Schicht. Im Anschluss sind nur noch Nacharbeiten nötig. Das muss aber nicht zwangsläufig geschehen. Der Materialeinsatz ist deshalb im Vergleich zu den gängigen Produktionsmethoden bei weitem geringer. Gibt es beim Fräsen bei bestimmten Körpern einen Materialschwund bis zu 80 %, beträgt er beim additiven Fertigen – zum Beispiel mit DED-Arc – oft nur 20 %, die bei der Nacharbeit entstehen.
„Führen wir uns ein plakatives Beispiel vor Augen: Der abgebildete Metallpropeller wurde mit dem Metall-3D-Druck gefertigt. Wäre er aus einem Block gefräst worden, hätte dieser ein Ausmaß von 60 x 90 x 90 cm bei einem Gewicht von rund 4 t gehabt, während das fertige Bauteil nur knapp 100 kg wiegt“, so Roithinger.
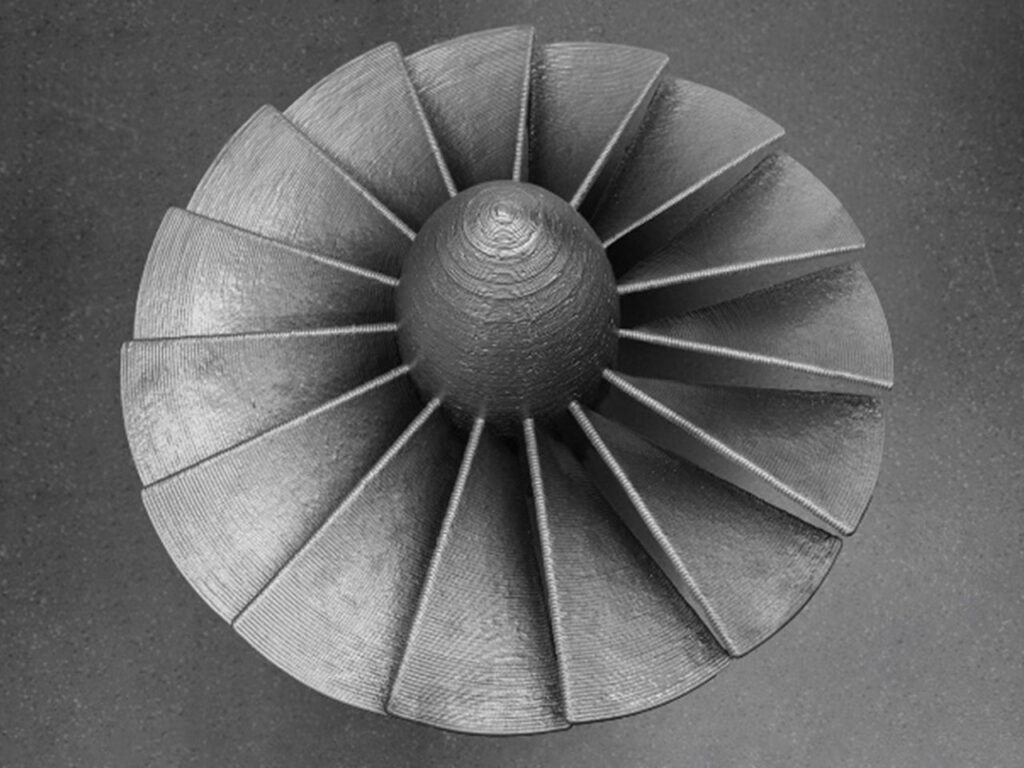
Die Zukunft von Metall-3D-Druck bei Fronius – ein Ausblick
„Das additive Schweißverfahren hat enormes Potenzial. Aber wie immer, wenn neue Technologien auf den Markt kommen, braucht es etwas Zeit, bis sie Akzeptanz und die geeigneten Anwendungen finden und zu boomen beginnen. DED-Arc ist im Vergleich zu anderen 3D-Methoden noch jung“, erörtert Roithinger. „Beim Wiederaufbau und bei der Reparatur beschädigter Teile gibt es aber schon jetzt großen Bedarf. Mit dem Metall-3D-Druck können wir die Lebensdauer von Komponenten – zum Beispiel Propeller oder Förderschnecken – um Jahre verlängern. Aber nicht nur das: Alle möglichen Ersatzteile sind on demand druckbar. Viele Gewerbe- und Industriebetriebe werden von Ort und Lieferzeit unabhängig. Das macht sie wettbewerbsfähiger – und zwar entscheidend. Außerdem sparen sie unnötige Lagerkosten.“
Um die Vielfalt der Anwendungsmöglichkeiten beim Metall-3D-Druck zu steigern und noch mehr Prozessstabilität zu erreichen, sind die Fronius Ingenieurinnen und Ingenieure dabei, den additiven Prozess auf ein neues Level zu heben. „Die Vision besteht darin, dass wir früher oder später sofort nach der Konstruktionsphase in den Druck gehen und der 3D-Drucker das perfekte Ergebnis ausspuckt. Hat sich die Technik erst einmal etabliert, wäre es denkbar, dass anstelle von Bauteilen einfach nur digitale Rezepte verschickt werden. Diese würden dann die benötigte Druckanleitung mit Schweißpfad, Schweißparameter, Wartezeiten und anderen Informationen enthalten. Kundinnen und Kunden müssten das digitale Rezept nur noch auf den Bordcomputer der automatisierten Anlage – das Leitsystem – hochladen und auf die Printtaste drücken“, gibt Roithinger einen abschließenden Einblick in die Gedankenwelt des Fronius Innovationsteams.
Keine Kommentare