Millionenfach praxiserprobt, eingespielte Handhabung und sehr hohe Nahtqualitäten: Warum sollte man WIG-Schweißgeräte also noch verbessern? Eine klare Antwort darauf geben wir mit der iWave-Serie: Die Multiprozess-Schweißgeräte sind gleichermaßen für WIG- und MIG/MAG-Schweißen geeignet, zu 100 % bereit für „Industrie 4.0“ und bieten deutlich optimierte Schweißprozesse. Doch wie wurde aus den ersten Ideen für ein neues WIG-Schweißgerät ein marktreifes Multiprozess-System?
Was muss ein WIG-Schweißgerät der neuen Generation können, damit es in Zukunft zu den Top‑Geräten am Markt zählt? Das wissen diejenigen am besten, die diese Geräte täglich nutzen: unsere Kundinnen und Kunden. Ihre Wünsche, Vorstellungen und Erfahrungen flossen von Beginn an in die Entwicklung der neuen iWave ein. Insgesamt 120 Projektmitarbeiterinnen und -mitarbeiter waren an diesem Projekt beteiligt: von den verschiedenen R&D-Fachbereichen wie Lichtbogentechnik oder Simulation über die Software-Entwicklung bis hin zu den Bereichen Produktmanagement, Service und Produktion.
WIG-Schweißen optimieren
„Wir haben seit Beginn unserer Entwicklertätigkeit danach gestrebt, sämtliche Schweißprozesse deutlich zu verbessern. Was bei dem hohen technischen Niveau von bestehenden WIG-Schweißgeräten keine allzu einfache Aufgabe war“, betont Paul Hofer, der als technischer Produktmanager wesentlich an der Entwicklung der neuen iWave beteiligt war. „Sehr früh beschäftigten wir uns in diesem Zusammenhang mit neuartigen Zündeigenschaften, der Entwicklung einer besonders guten AC-Performance und neuen WIG-Prozessen, die Schweißern eine Vielzahl von neuen Möglichkeiten erschließen sollen“, ergänzt Hofer.
Ziemlich schnell stellte sich heraus, dass „Multiprozessfähigkeit“ ein zentrales Thema ist: „Als technische Basis für die neue iWave hat sich unsere TPS/i-Plattform für MIG/MAG-Schweißgeräte angeboten. Rasch war für uns deshalb klar, dass wir ein Schweißgerät entwickeln werden, das neben einem rundum optimierten WIG-Prozess auch andere Schweißprozesse, wie das MIG/MAG-Schweißen, gleichwertig und ohne Qualitätseinschränkungen beherrscht“, erklärt Stefan Aichinger, Projektleiter der iWave-Entwicklung. „Im Endeffekt hatten wir uns vorgenommen, als erster Qualitätsanbieter die sprichwörtliche ‚eierlegende Wollmilchsau‘ zu kreieren – also ein vollwertiges Kombi-Schweißgerät“, so Aichinger weiter.
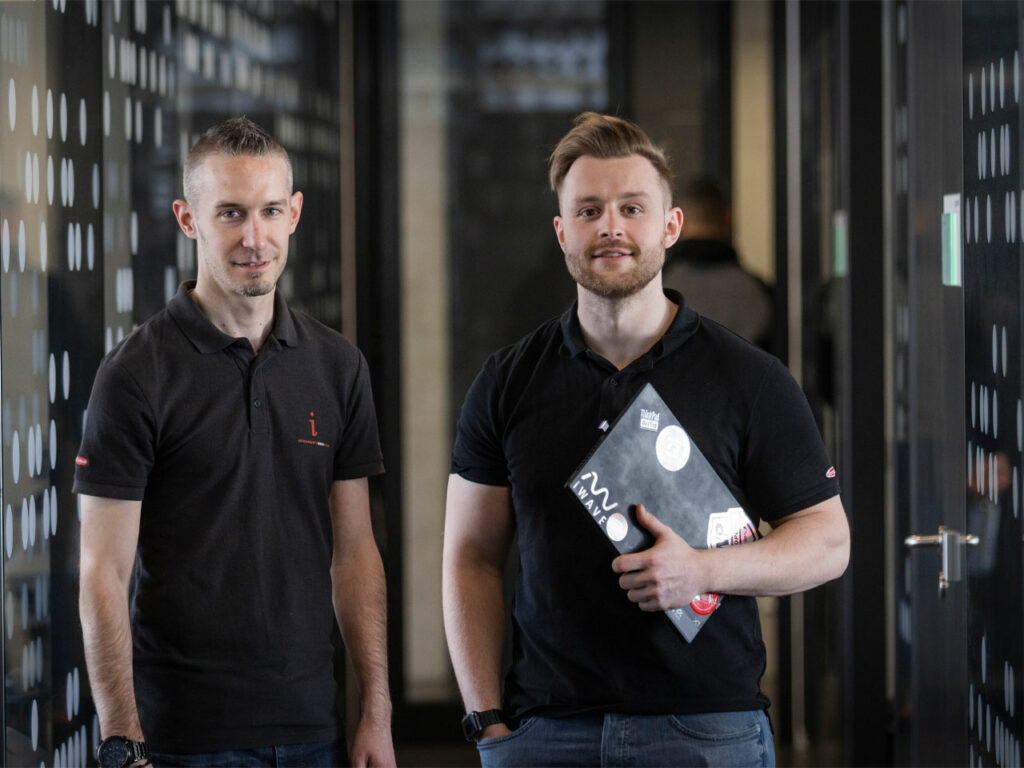
Wie also muss man sich den Entwicklungsprozess der iWave vorstellen? Grundsätzlich lässt sich dieser in 10 große Schritte einteilen:
Schritt 1: Das Lastenheft. Womit wollen wir unsere Kundinnen und Kunden begeistern?
180 Seiten stark gibt das Lastenheft Antworten auf die Fragen, die wir uns nach vielen Kundengesprächen und Marktrecherchen gestellt haben:
- Wie können wir die Qualität aller Schweißprozesse, die die iWave abdecken soll, noch besser machen?
- Welche Voraussetzungen sind für ein Multiprozess-Schweißgerät notwendig, damit es sich kompromisslos sowohl für WIG- als auch MIG/MAG-Schweißen eignet?
- Wie intuitiv muss die Benutzeroberfläche der Zukunft gestaltet sein?
- Welche Anforderungen für Industrie 4.0 müssen erfüllt sein?
- Welche Herausforderungen haben wir hinsichtlich der Modularität des Systems und wie können wir das Gerät so konzipieren, dass es unseren Planeten schont?
Schritt 2: Das Pflichtenheft. Und wie machen wir es?
Im Pflichtenheft haben wir festgelegt, auf welche Art und Weise sich Wünsche und Anforderungen realisieren lassen. Technische Lösungsansätze und Konzepte wurden bis ins Detail ausgearbeitet. Eine besondere Herausforderung war das Steuerungssystem: Unterschiedliche Bauteile, drei Schweißarten mit ihren verschiedenen Varianten und alle dazugehörigen Schweißprogramme mussten in der Steuerungs-Software perfekt aufeinander abgestimmt werden.
Gleichzeitig sollte die iWave eine intuitive, selbsterklärende Bedienoberfläche bekommen. „Wir entwickelten für die iWave ein ‚grafisch-dynamisches‘ Bedienkonzept mit Touchscreen. Dadurch sehen die Schweißer mittels Grafiken auf den ersten Blick, welche Prozesse und Parameter sie eingestellt haben. Zudem bekommen sie eine direkte Rückmeldung, wie sich eine Schweißnaht aufgrund der vorgenommenen Einstellungen verändert“, erklärt Paul Hofer.
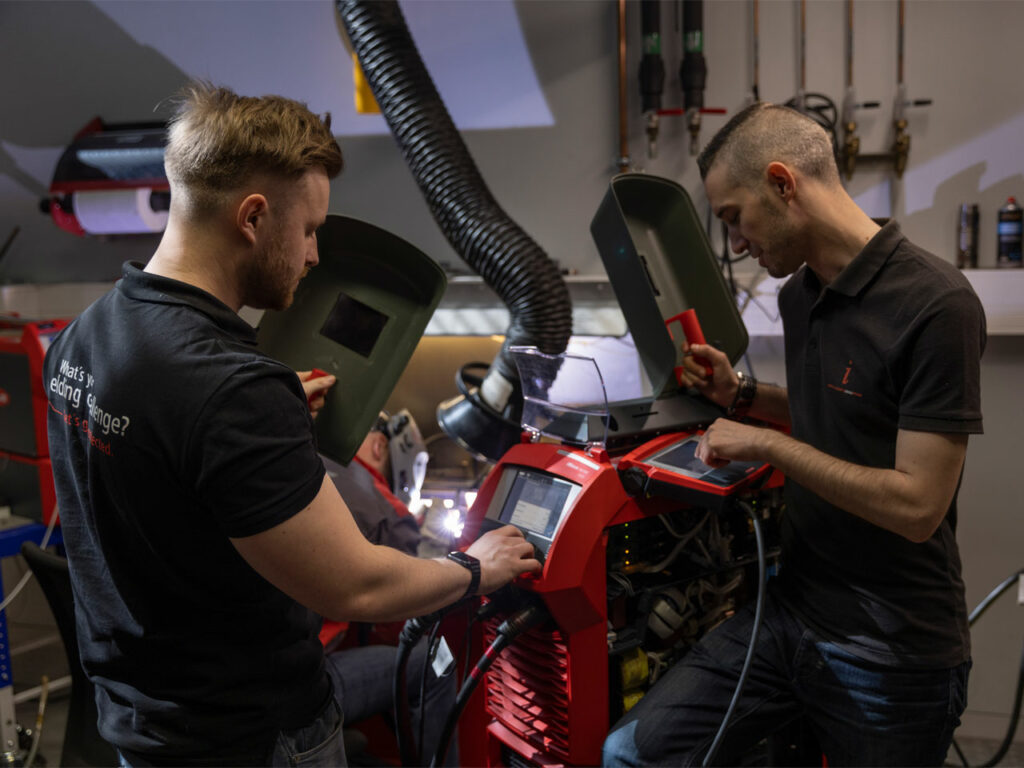
Schritt 3: Prototypen bauen – Ideen und Konzepte werden real
Im darauffolgenden Schritt wird die iWave endlich real „greifbar“. Auf Basis der im Pflichtenheft detailliert beschriebenen Technologien baut das Projektteam die ersten Prototypen bzw. eine Vorserie der iWave.
Schritt 4: Praxistests bei Kundinnen und Kunden – keine Einschulung für Schweißfachkräfte!
Wenn eine Vorserie zu 100 Prozent perfekt wäre, wäre sie keine. Deshalb haben wir die Prototypen der iWave umfassenden Tests unterzogen. Natürlich intern – aber auch im weltweiten Praxis-Einsatz: zum Beispiel in Auslandsniederlassungen, bei Repräsentanten und bei langjährigen Kundinnen und Kunden. Um das selbsterklärende Bedienkonzept „aufs Exempel“ zu testen, gab es für die Schweißerinnen und Schweißer bewusst keine Einschulung zu den neuen Geräten. Wie das wohl angekommen ist?
Schritt 5: Wir hören unseren Anwenderinnen und Anwendern zu – Prototypen verbessern
In diesem Schritt geht es darum, die Rückmeldungen zu den Prototypen zu analysieren, richtig einzuordnen und in den weiteren Produktentwicklungsprozess einfließen zu lassen. Besonders positiv verlief das Kunden-Feedback für die Entwicklerteams in Zusammenhang mit der Schweißperformance und der sehr einfachen Bedienung.
Schritt 6: Produkttests – harte Hammerschläge, Staub und mehr
Nun werden die „Samthandschuhe“ ausgezogen: Die neuen Geräte müssen unter anderem eine Schlagprüfung mit Hammerschlägen, eine Fallprüfung aus einer bestimmten Höhe und einen Metallstaub-Test erfolgreich bestehen. Zudem wurde das Kälteverhalten der iWave auf bis zu -40 Grad erfolgreich getestet. Warum haben die Fronius Mitarbeiterinnen und Mitarbeiter ihre iWave derart brutal gequält? Einerseits, um den strengen internen Qualitätsrichtlinien gerecht zu werden, andererseits aber auch, um Zertifizierungen und Zulassungen für bestimmten Märkte zu erhalten.
Schritt 7: Design-Freeze – endlich fertig mit der iWave?
„Endlich fertig mit der iWave!“ können zumindest viele Mitglieder der beteiligten Entwickler-Teams an dieser Stelle sagen. „Design-Freeze“ bedeutet: Der Produktentwicklungsprozess ist erst einmal abgeschlossen – es werden bis auf weiteres keine Änderungen an den neuen Multiprozess-Schweißgeräten mehr vorgenommen. Doch was kommt als nächstes?
Schritt 8: Nullserie – Generalprobe für die Produktion
Jetzt übernehmen die Fronius Produktionstechnikerinnen und -techniker die Hauptaufgaben: Sie richten die Produktionsstraßen für die Serienfertigung der iWave ein. Die einzelnen Produktionsschritte werden unter Praxisbedingungen optimiert und effizient gestaltet. Damit im nächsten Schritt alles klappt, haben wir innerhalb von drei Monaten fast 60 Vorserien-Geräte der verschiedenen iWave-Typen produziert.
Schritt 9: Hochlauf – die Serienproduktion beginnt
Fast am Ziel: Die Serienfertigung der iWave startet, die Produktion wird Schritt für Schritt hochgefahren.
Schritt 10: Start of Sales – und los geht’s!
Es ist der 19. Januar 2022 – die neue iWave wird offiziell am Markt präsentiert. Das Verkaufs- und das Marketing-Team von Fronius übernehmen an dieser Stelle zentrale Aufgaben. Sie tragen dazu bei, dass der jahrelange Einsatz der Entwicklerteams und die Arbeit der Produktionsmitarbeiterinnen und -mitarbeiter auch am Markt zum Erfolg wird.
Mit dem Verkaufsstart geht ein Entwicklungsprozess zu Ende, in den eine Menge Zeit, Geld und Energie geflossen sind. Doch letztendlich zählen die Ergebnisse – und die ganz konkreten Vorteile und Highlights, welche die neue iWave beim Schweißen bietet.
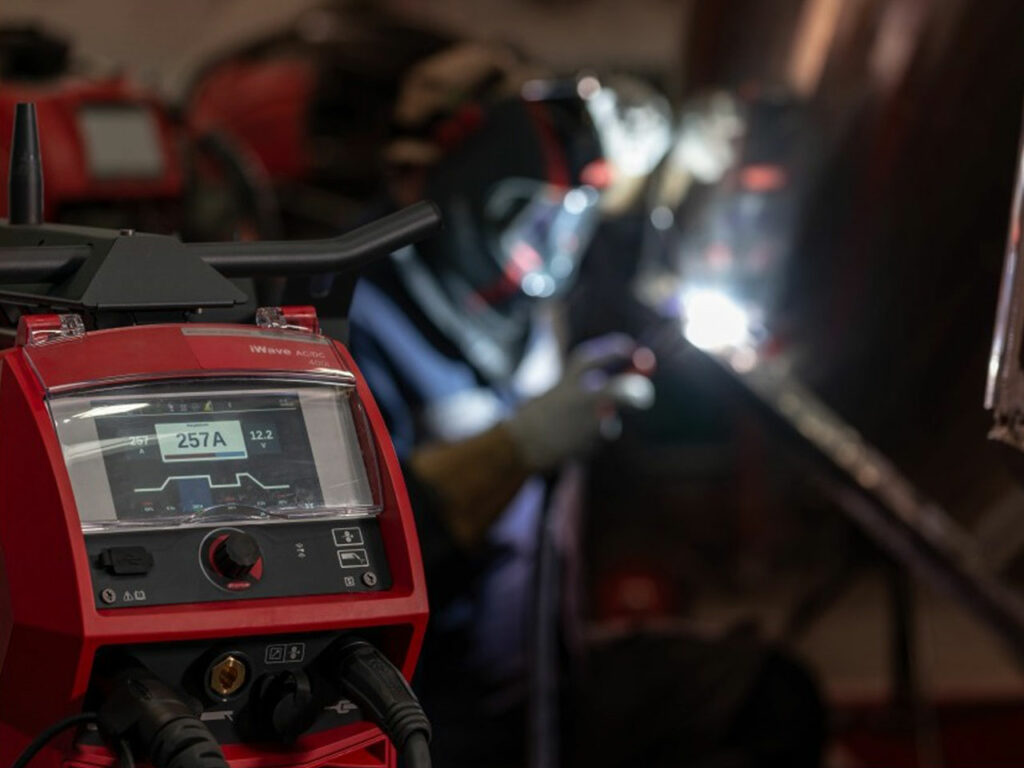
Entwicklung endet nie
„Besonders glücklich sind wir darüber, dass wir alle im Lastenheft definierten Anforderungen in die Realität umsetzen konnten – was unsere jahrelange Arbeit natürlich bestätigt hat“, freut sich iWave-Projektleiter Stefan Aichinger. Wirklich abgeschlossen ist ein Entwicklungsprozess bei technischen Produkten wie Schweißgeräten aber ohnehin nie: Nach dem erfolgreichen Markt-Eintritt betreut das Fronius Life-Cycle-Team die iWave in allen technischen Belangen. Während des gesamten Produktlebenszyklus der iWave wird es regelmäßig kleinere und mitunter auch größere Adaptionen geben.
Und was machen die zahlreichen Technikerinnen und Techniker, die an der Entstehung der neuen iWave beteiligt waren, jetzt? Fakt ist, dass ihnen die Aufgaben nicht so schnell ausgehen werden: Wir möchten unser Premium-Portfolio im Bereich der WIG-Schweißgeräte neugestalten – und mit der iWave ist der erste Meilenstein schon einmal geschafft.
Wer mehr aus der persönlichen Perspektive von Projektleiter Stefan Aichinger und dem technischen Produktmanager Paul Hofer über die Entwicklung der neuen iWave erfahren möchte, kann sie im Fronius Podcast zum Thema iWave-das intelligente WIG-Schweißgerät hören.
Keine Kommentare