Hour after hour, five days a week: anyone whose job involves MIG/MAG welding can’t help but know welding torches inside out. So what exactly makes a good welding torch? Is what qualified welders regularly reach for at work really the optimum solution? These are the sort of questions that are explored by the developers of welding torches. We took a look over their shoulder and now explain how new welding torches come into being and why the human factor plays such a key role here.
It’s not only the power source, the arc, and the workpiece that come together at the front of the welding torch. The handle of the torch also acts as the link between man and machine – an extension of the user’s arm, so to speak.
But what do welders expect from a new welding torch? Let’s deal with a basic aspect right away: with manual welding torches it’s not just a question of well-functioning technology, outstanding welding power, and a long service life for wear parts.
At least equally important are ease of use, ergonomic design, and the feel of the tool, for example, how well a welding torch fits into the hand, how easy making settings is – and last but not least, how the new welding torch appeals to welders, i.e., whether they like it.
Regional variations in welding torches
A look round the globe reveals differences in designs. While small, lightweight welding torches are preferred in Asian countries, many welders in the USA rely on heavy torches that are very solid in design. When it comes to the size of welding torches, Europe falls in between – with European standards becoming increasingly important, including at a global level.
New development of welding torches: who’s behind this?
Welding torches have existed for over a century – yet every year new models appear on the market. There are four key reasons behind new developments:
1) Because customers want them
A change in customer requirements is arguably the most important reason behind innovations involving welding torches. Companies facing new challenges approach the torch manufacturers and ask them to think up appropriate solutions, for example, to access awkward corners with an innovative procedure using a new welding torch.
2) New power source + new welding torch = perfect welding system
However, major impetus for new developments sometimes also comes from the welding technology companies. If a new series of power sources is being launched, this generally also involves developing new torch types that are perfectly geared to the technology of the new equipment. Welders will only get maximum benefit from technical innovations if there is perfect interaction between all areas of the system – from the welding torch to the power source.
3) Ideas from research and development departments
Good ideas are not always prompted by a specific cause or event. In the case of welding torches, technical innovations often emerge when design engineers give free rein to their creativity and come up with something new.
4) Normative requirements on welding torches: because it’s the law
There’s one thing behind welding torch innovations that can’t be ignored: last but not least, changes to the normative requirements – i.e., the amendment of statutory provisions. One clear example of this is the development of welding torches with an extraction system after the EU tightened up the health and safety regulations for welders. This means that, in certain regions, selling torches without such extraction systems is now pretty difficult.
Welders decide whether a welding torch will sell
There aren’t many parts of a welding system where the human factor is so important as in the case of the torch. At the end of the day, it’s the users who decide whether a newly developed welding torch will be a big seller or get left on the shelf. They simply either recognize the benefits of the new torch and start using it in their daily work or stick by their existing trusty model that has done sterling service over the years.
This is how a welding torch is developed: 5 steps
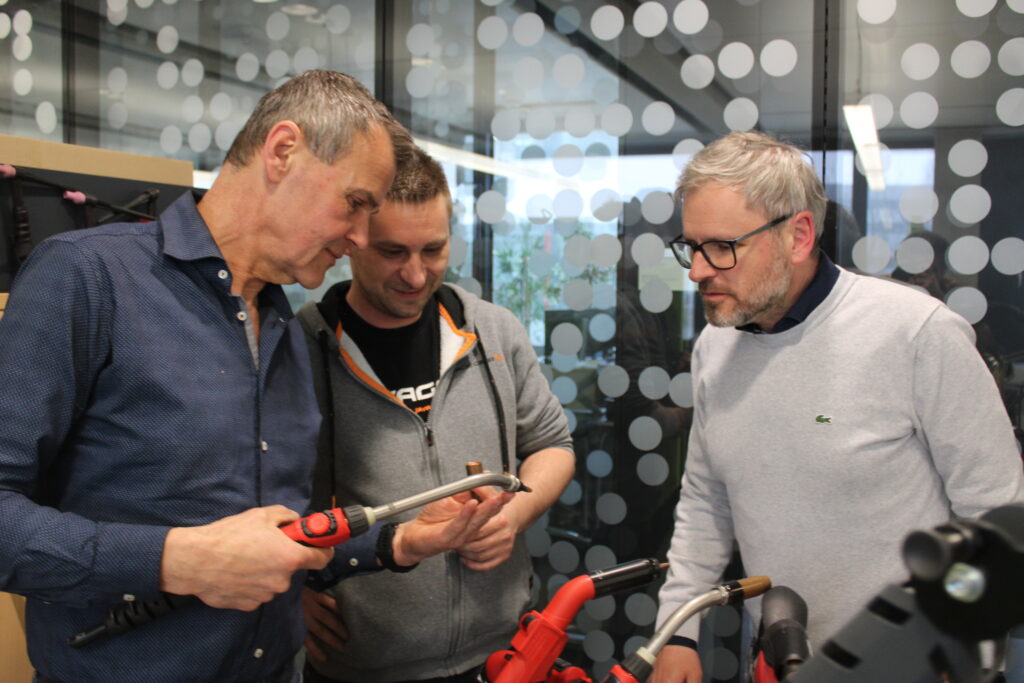
How a welding torch is developed of course depends on the individual company. Greatly simplified, the development process can be outlined with the following steps:
Step 1: Concept phase
To start with, all requirements the new welding torch has to fulfill are summarized in a requirements specification. Development can then start. The engineers in the Development departments sit down at their PCs and get down to designing.
Well-equipped welding technology companies will have already produced 3D models of the new torch that are purely digital. These virtual welding torches then undergo detailed testing in simulators, which are high-performance computers specially equipped for this purpose. Such virtual trials allow most of the processes that take place in real welding torches to be accurately reproduced using thermal, hydraulic, and aerodynamic simulations.
Step 2: Prototypes – the first reality check
If it’s no longer possible to improve the design using the simulator, it at last becomes the “real thing”. This is when the first prototypes come into being. They may well look a bit rough and ready on the outside, but should already fulfill all the technical requirements on the new welding torch.
Whether this is actually the case will then be tested during in-depth trials. An arc technician checks the quality of the arc and the welding processes. Thermal imaging cameras and temperature sensors are used to record and optimize temperature distribution, while the gas flows at the torch can be visualized with striation optics. This helps, for example, to improve welding quality and maximize the service life of contact tips and gas nozzles.
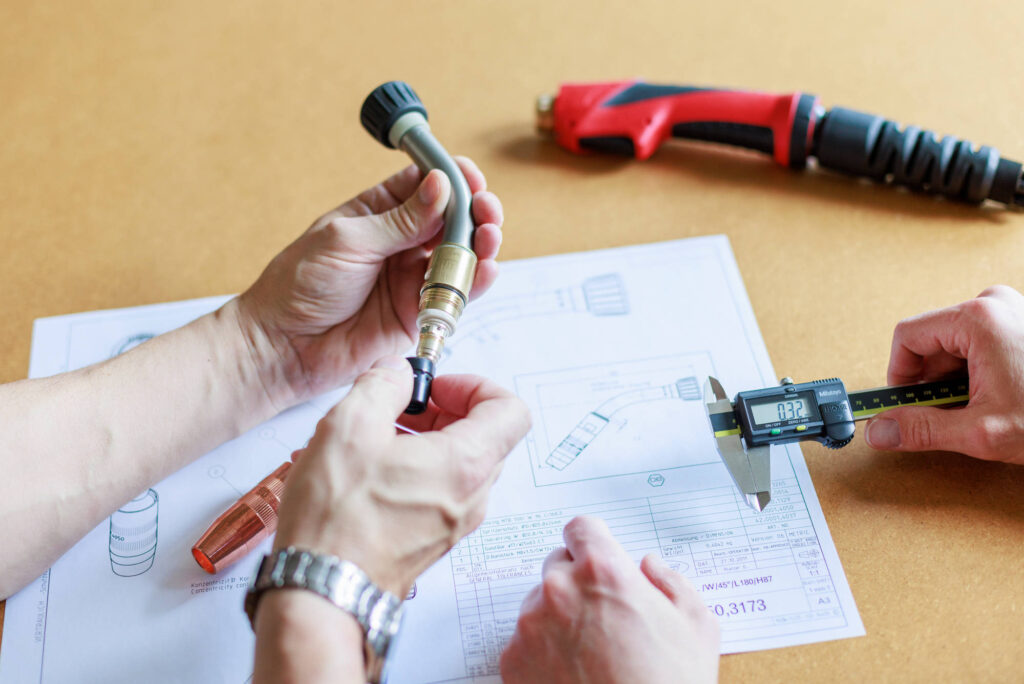
Step 3: Performance specification and preproduction series
After prototype testing, the project team then generally draws up the performance specification, defining all properties of the new welding torch. Detailed development can now start. The tools required for series production are built while the manufacturing processes are determined in parallel.
Preproduction series are also run for welding torches so every detail of them can be rigorously tested, both by the company and externally. While in-depth functional checks and load tests are carried out by the manufacturers, preproduction welding torches are often sent out to selected customers. Their welders try them out by using the new torches in their work.
Step 4: Decisive customer feedback on the welding torch
Customer feedback is of key importance for welding torch manufacturers, not least as regards ease of use and the ergonomic design of their devices. The views of welders about a new torch model are sometimes also sought with the help of questionnaires.
Step 5: Design-freeze – handing over to the production technicians
Occasionally several feedback loops from different company departments and key accounts are needed until a product has been perfected. Once a welding torch can no longer be improved any further in the eyes of its developers, this is followed by the design freeze. Product development is now complete, and the production technicians take over, setting up the plant for series production.
The steps described here are of course merely a rough outline of the stages involved in developing a new welding torch. If you’d like to learn more about the product development processes for welding systems, you can also find information in the article “From TIG Welding System to Multiprocess Welding System: The Development of the New iWave Series in 10 Steps”.
Conclusion: When it comes to welding torches, it’s welders who count
“All welding torch development at Fronius revolves around the welders. Their visions and wishes have a major impact on our entire development process,” explains Manfred Hubinger, Product Line Manager Welding Torches at Fronius.
“Good torch developers always make sure that welders are happy with them. Besides cutting-edge technology and reliability, it’s first and foremost properties such as ease of use and the right ergonomic design that make a manual welding torch outstanding. It has to be simple to operate – and fit in the hand well,” sums up Christian Aitzetmüller, Product Manager Welding Torches at Fronius.
Has our article awakened your interest and you’d like to find out more about Fronius welding torches? Then take a look at our website right away! There you can find all the technical details and information about what you need for your individual requirements.
1 Comment
imechinstitute
10. August 2023 at 11:14Impressive insight into Fronius’ customer-centric approach to welding torch development. Prioritizing welder satisfaction and ergonomic design showcases their commitment to excellence. 👏🔧