Was tun, wenn in der schweißtechnischen Produktion Bauteile in hoher Stückzahl gefertigt werden müssen? Roboterschweißzellen sind die Lösung. Die Anforderungen an die Ausführung solcher Schweißzellen sind jedoch riesig: Unterschiedliche Bauteile in Form, Gewicht und Größe verlangen nach spezifischen Lösungen.
Und trotzdem – die zentralen Aufgaben von Roboterschweißzellen wiederholen sich permanent, unabhängig vom Bauteil. So gehören zum Beispiel die Bauteilpositionierung, der Kontaktrohrwechsel oder die Brennerreinigung zum Standardrepertoire. Konstrukteure müssen das Rad deshalb nicht ständig neu erfinden. Bei der Konzeption moderner Roboterschweißzellen greifen sie auf eine Kombination verfügbarer Module zurück – auch im Sinne der Nachhaltigkeit. Alles, was die Spezialisten dafür benötigen, ist eine Plattform. Also ein Baukastensystem aus standardisierten und spezialisierten Komponenten.
Leistungsfähige Engineering-Software
Für das Engineering von Roboterschweißzellen steht potente Software zur Verfügung. Diese beinhaltet umfangreiche Bibliotheken aus standardisierten Modulen für die gesamte Roboterperipherie. Standardelemente wie Roboter-Fahrbahnen, Stative oder Drehtische müssen die Konstrukteure daher nicht jedes Mal neu entwerfen. Vielmehr können sie ihr Augenmerk auf das Lösen zentraler Kundenanforderungen richten: zum Beispiel eine geeignete Spannvorrichtung zu entwickeln oder die richtige Schweißfolge zur Vermeidung von Bauteilverzug festzulegen. Ein weiterer Vorteil von Baukastensystemen liegt in ihrer höheren Wirtschaftlichkeit. Denn weniger Entwicklungs-Aufwand spart Kosten, was letztlich die Preise und somit den Finanzierungsbedarf beim Kunden reduziert.
3-D-Konstruktion einer Roboterschweißzelle inkl. Bauteil, Schienenfahrzeugbau
Module und ihre Funktionen
Die Module erfüllen also individuelle Anforderungen der Kunden und somit wichtige Funktionen eines Roboterschweißsystems. Diese Module werden in Baugruppen, Unterbaugruppen und Komponenten unterteilt. Sie können mit Blick auf den künftigen Bedarf vorgefertigt werden; virtuell für die Bibliothek der Engineering-Software und physisch für den Produktionsbedarf von Roboterschweißzellen.
Beispiele für Schweißzellen-Module
/ Modul Schweißen (Schweißstromquellen, Drahtvorschub, Brenner,…)
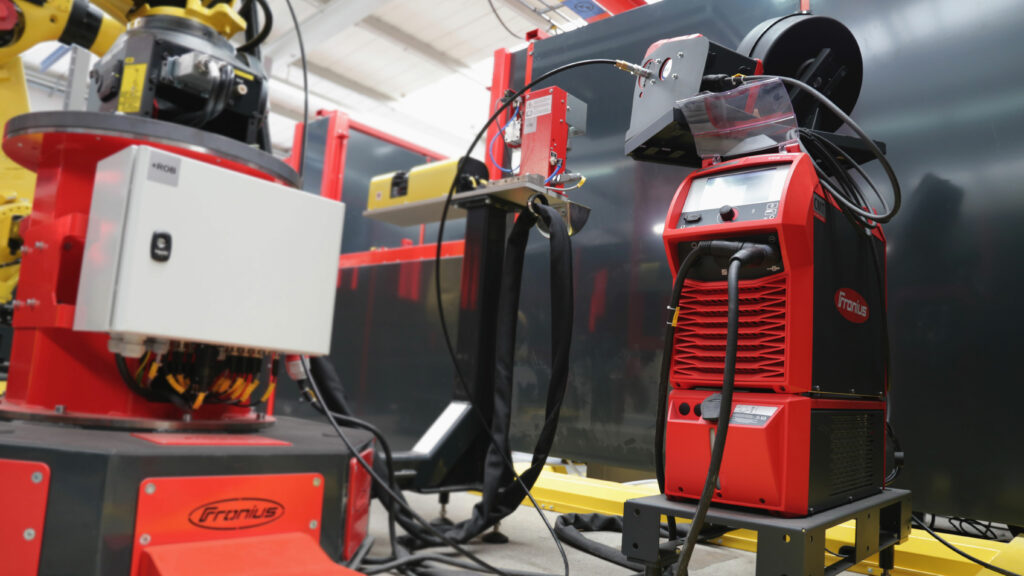
/ Modul Bauteil positionieren (Positionierer, Handling-Roboter, Fahrbahn, C-Galgen, Stativ, …)
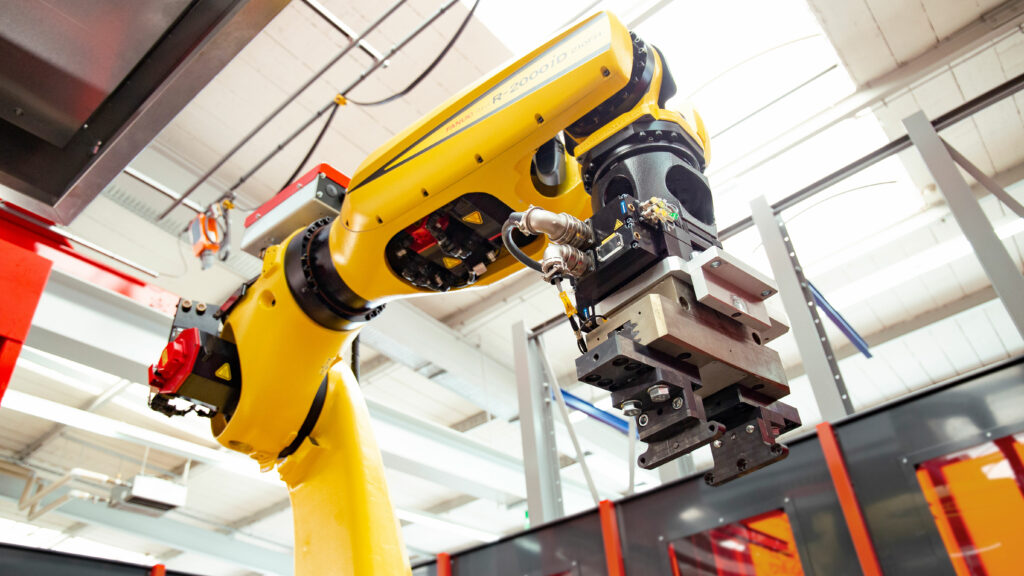
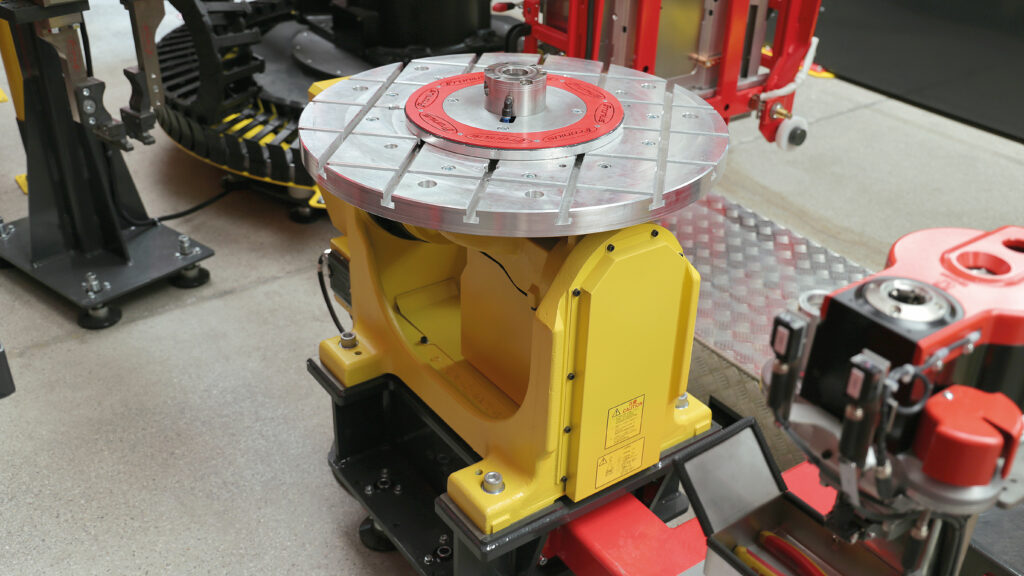
/ Modul Roboter positionieren (Linearachse, C-Galgen-Portal, …)
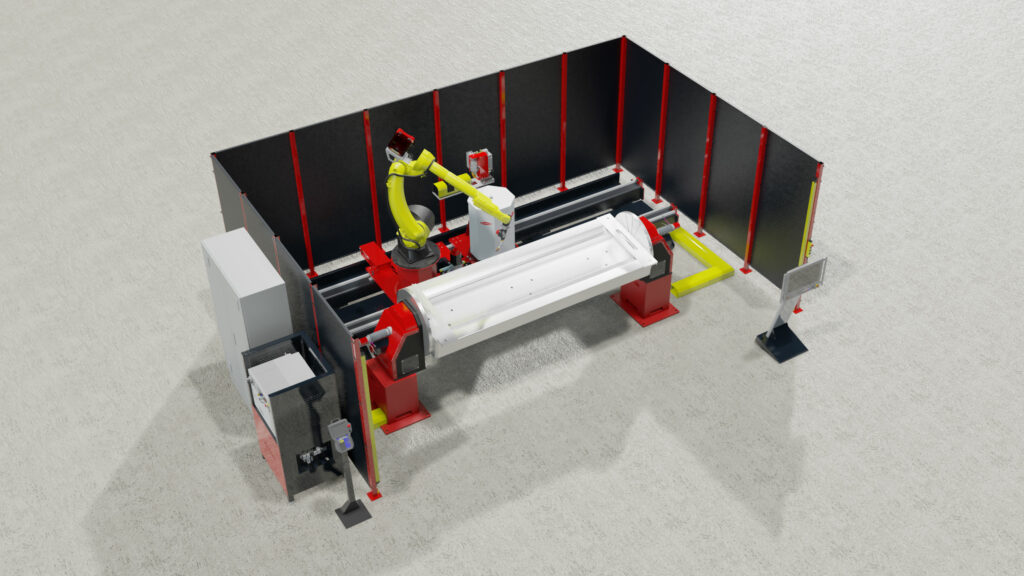
/ Modul Bauteil zuführen (Schleuse, Förderband, …)
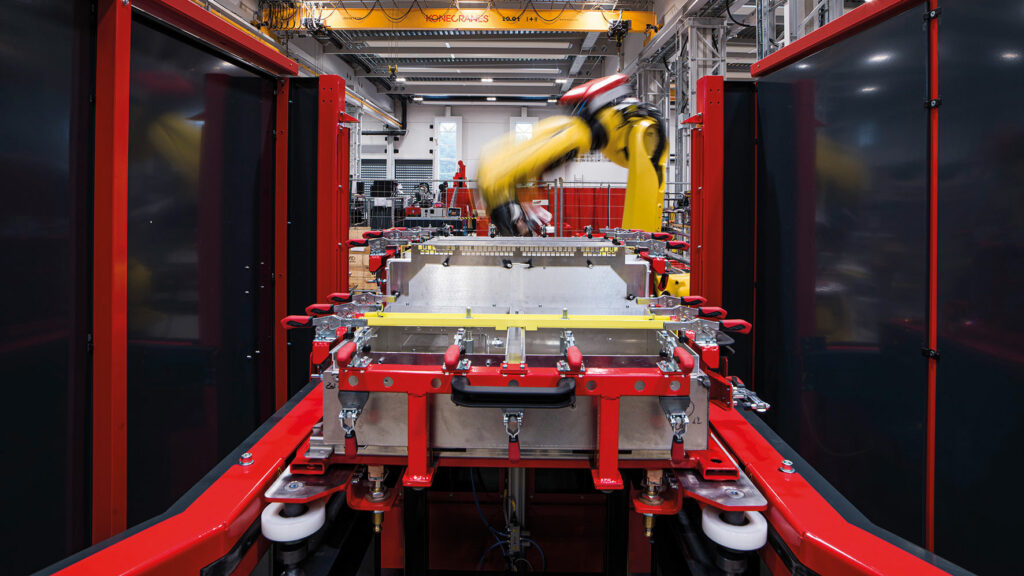
/ Modul Sicherheit (Schutzzaun, Lichtvorhang, Lichtgitter, Rollvorhang, …)
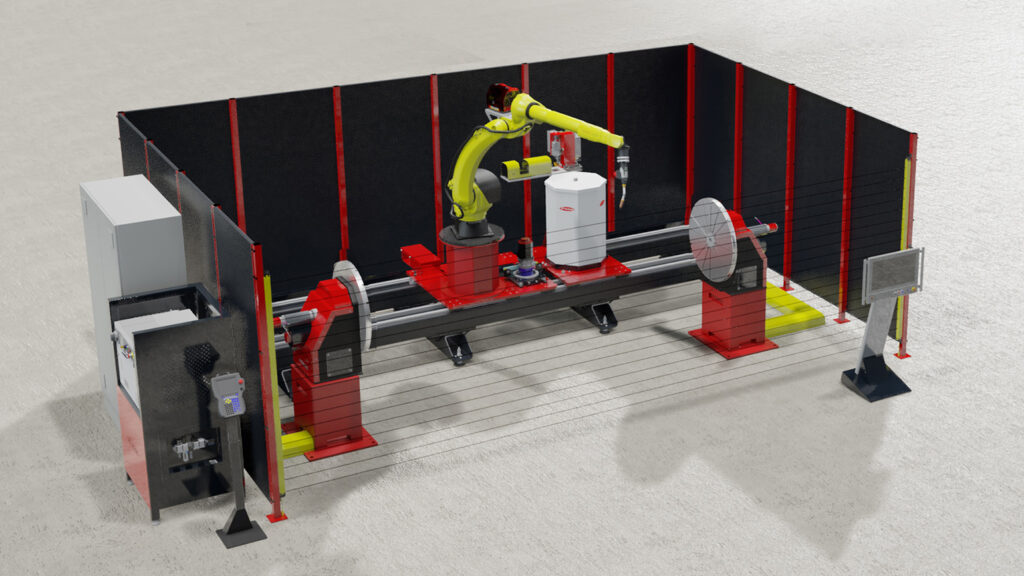
/ Modul Brenner positionieren (Roboter)
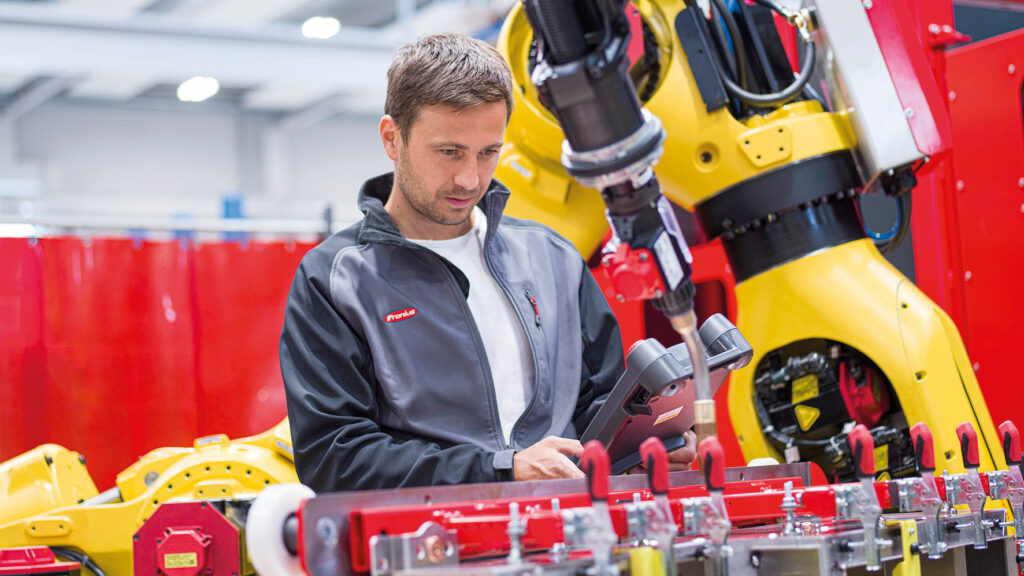
/ Modul System steuern (Schaltschrank, HMI-Systemsteuerung)

Die Funktionen der Module können durch diverse Optionen wie Sichtfenster, Kabelaufroller für Fernregler, Blendschutz-Varianten und andere erweitert werden.
Schweißroboter und Dimensionierung
Präzision und Wiederholgenauigkeit beim Schweißen sind die typischen Stärken der Schweißroboter. Möchte man neben hochwertigen Schweißnähten auch die Flexibilität bei Bauteilen sowie die Schweißfolgen sicherstellen, sollte man in puncto Design, Reichweite und Tragfähigkeit vorausschauend planen:
Wenn kleine Standflächen mit schlanken Roboterarmen und langen Reichweiten kombiniert werden, kann auch in engen Räumen geschweißt werden. Typische Beispiele sind Achsen, Halterungen, Sitze, Auspuffanlagen, Chassis-Träger, Kranaufbauten, Tank- und Rohrleitungskomponenten.
Verwendet man schwere Brenner, wie beim Widerstandspunkt- oder Laser-Hybrid-Schweißen, benötigt man Roboter mit hoher Tragfähigkeit.
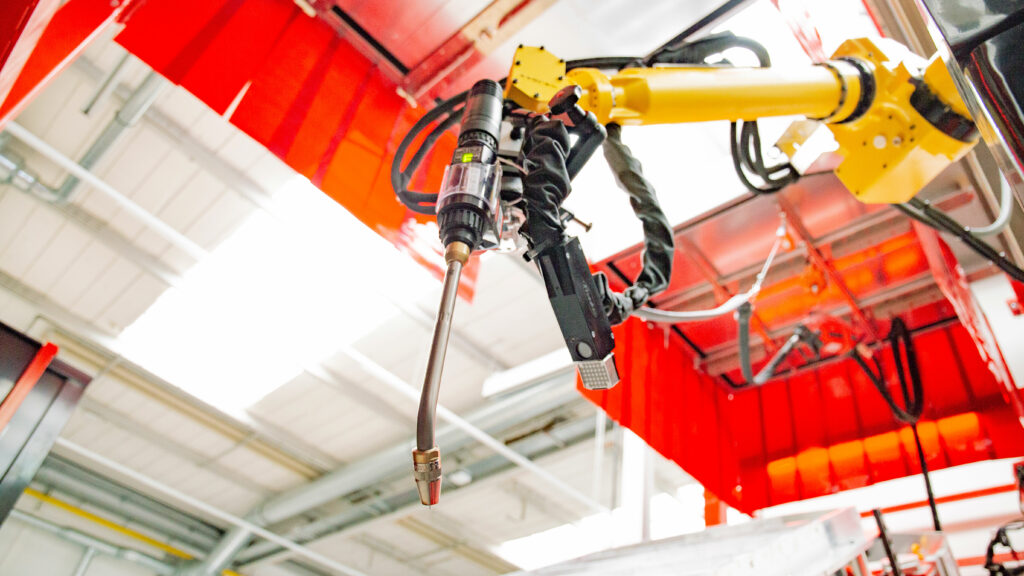
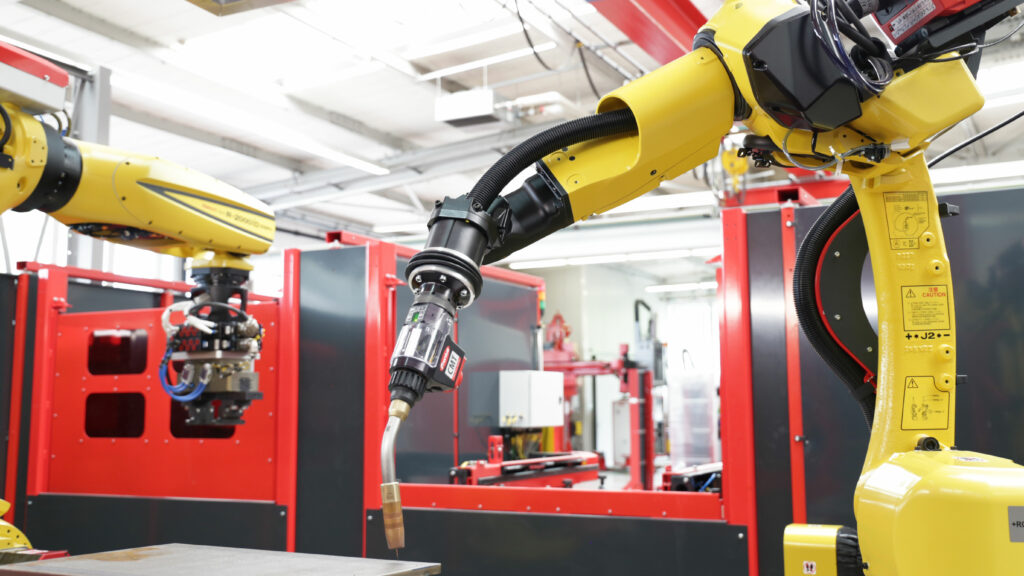
Vermeiden von Kabelstörungen
Handgelenk-Roboterachsen mit Hohlwellen erlauben es, Steuer-, Sensor- und Versorgungsleitungen im Inneren der Achse zu führen. So wird vermieden, dass sich die in den Schläuchen gebündelten Leitungen bei komplexen Bewegungsabläufen um die vorderen Roboterachsen wickeln. Ein weiterer Vorteil der Hohlwellenausführung: Potenzielle Kabelstörungen können softwaretechnisch simuliert werden.
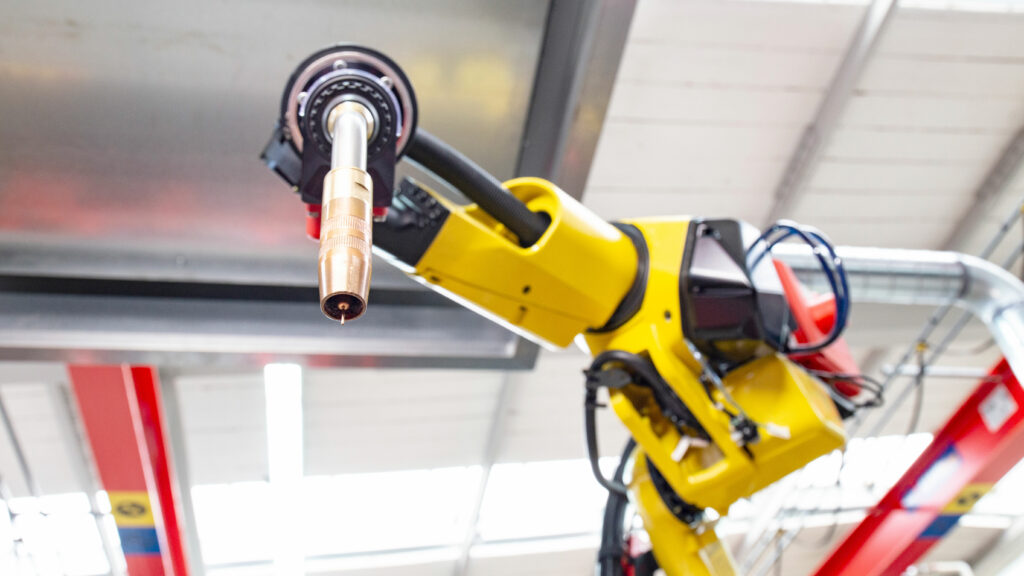
Alles unter Kontrolle
Sowohl für perfekte Schweißergebnisse als auch für die Sicherheit der Anlagenbediener müssen alle Module der Roboterschweißzelle präzise interagieren. Dafür sorgt in der Regel eine zentrale Systemsteuerung. Diese steuert und überwacht sämtliche Peripheriekomponenten wie Roboter, Schweißstromquelle, Positionierer, Regalsysteme, Brennerreinigung oder Lichtschranken.

…
Programmeditoren, Schweißdaten-Kontrolle und Benutzerverwaltung
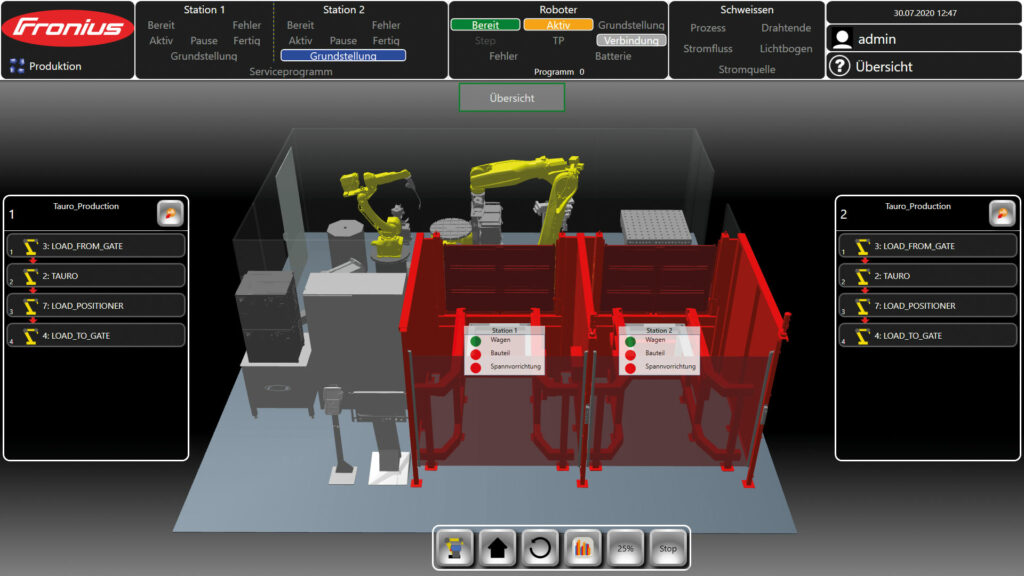
/ Moderne High-Tech-Systemsteuerungen brillieren mit intuitiven Programmeditoren. Hier definieren Schweißtechniker Schritt für Schritt die notwendigen Programmabläufe und speichern sie als Ablaufschrittketten. Diese werden dann einzelnen Bearbeitungsstationen zugewiesen.
/ Dreidimensionale Real-Time-Anzeigen visualisieren sämtliche Roboterbewegungen und Schweißarbeiten auf dem Monitor. Sie gewähren einen detaillierten Überblick über die Zustände von Peripheriekomponenten und Schutzbereichen – und zwar in Echtzeit!
…
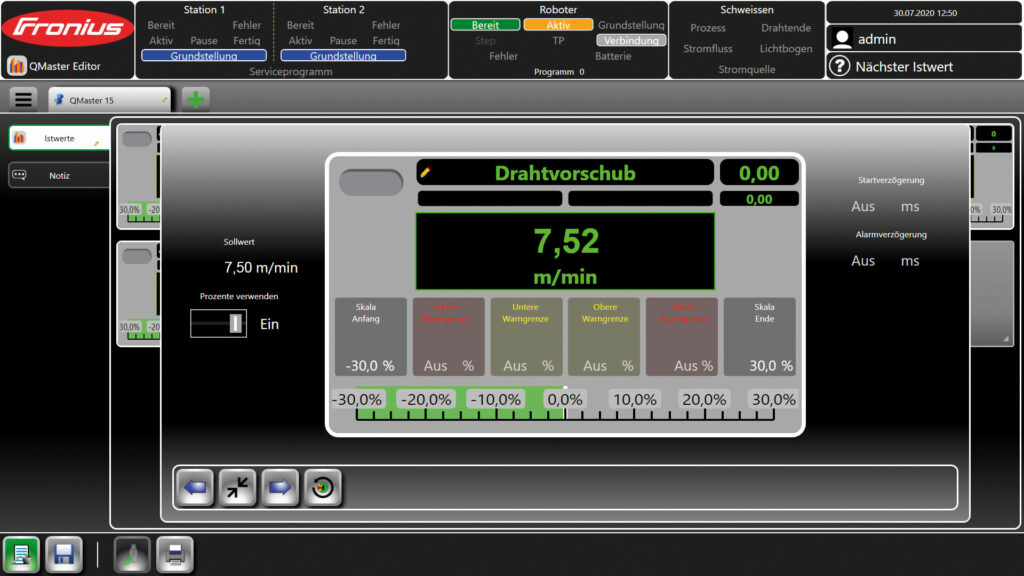
/ Kontrollfunktionen erlauben das Vorwählen von Warnschwellen und Fehlergrenzen. Zeitverzögerungen für Start und Alarm können ebenfalls eingestellt werden.
…
…
…
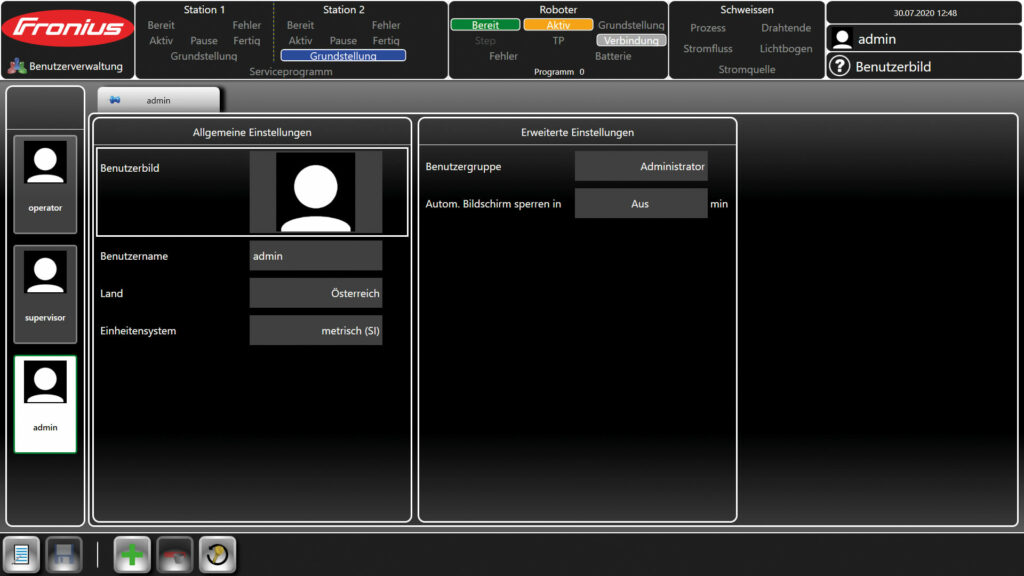
/ Benutzer werden in personalisierten Benutzerverwaltungen angelegt und editiert, Berechtigungen aufgabenbezogen vergeben. Bediensprachen und Einheitensysteme sind individuell einstellbar. Persönliche Passwörter sichern die gespeicherten Einstellungen.
…
Standardfunktionen
Standardmäßig umfassen viele Systemsteuerungen eine Benutzer- und Programmverwaltung, diverse Störmeldeanzeigen, Takt- und Stückzähler, Anlagenstatusanzeigen und eine Sprachumschaltung. Häufig verfügbar sind Schnittstellen zu gängigen ERP-Systemen und eine Web-API für den Datentransfer zu Drittsystemen.
Offline programmieren: Weniger Stillstandskosten, mehr Output
Effizienz und Output von Schweißarbeiten sind maßgebliche Indikatoren für die Wirtschaftlichkeit von Fertigungsprozessen. Doch wie können diese Faktoren gesteigert werden? Eine Möglichkeit ist, die Schweißabläufe offline zu programmieren – also getrennt von der Roboterschweißzelle. Somit können sie schon im Vorfeld bis ins Detail optimiert werden.
Roboterprogrammierer müssen somit nicht mehr auf das Ende von laufenden Schweißarbeiten warten. Stattdessen können sie den Roboter abseits der Anlage vom PC oder Laptop aus „teachen“ und anschließend den gesamten Schweißablauf offline simulieren: Schweißnaht für Schweißnaht.
Leistungsstarke Offline-Programmier- und Simulations-Software erkennt Achslimits, berechnet Startpunkte, Endpunkte sowie Anfahrtswege und setzt selbstständig Positionspunkte. Störkonturen werden visualisiert und Brenneranstellungen korrigiert. All das im Vorfeld und nicht erst während der Schweißarbeiten.
Autonomie und Sicherheit
Die digitale Vernetzung aller Module mit einer übergeordneten Systemsteuerung gewährleistet voll automatisierte Abläufe und sorgt so für ein hohes Maß an Autonomie im Workflow, sowohl im Bauteil-Handling als auch beim Schweißen. Manuelle Tätigkeiten werden eingespart, der Bediener kann sich auf das Wesentliche konzentrieren. Ein weiterer Vorteil der Anlagenautonomie liegt in der erhöhten Sicherheit des Operators. Rauchgasabsaugungen, Schutzeinhausung, Lichtschranken oder Not-Aus-Taster verhindern gesundheitliche Schäden und Verletzungen.
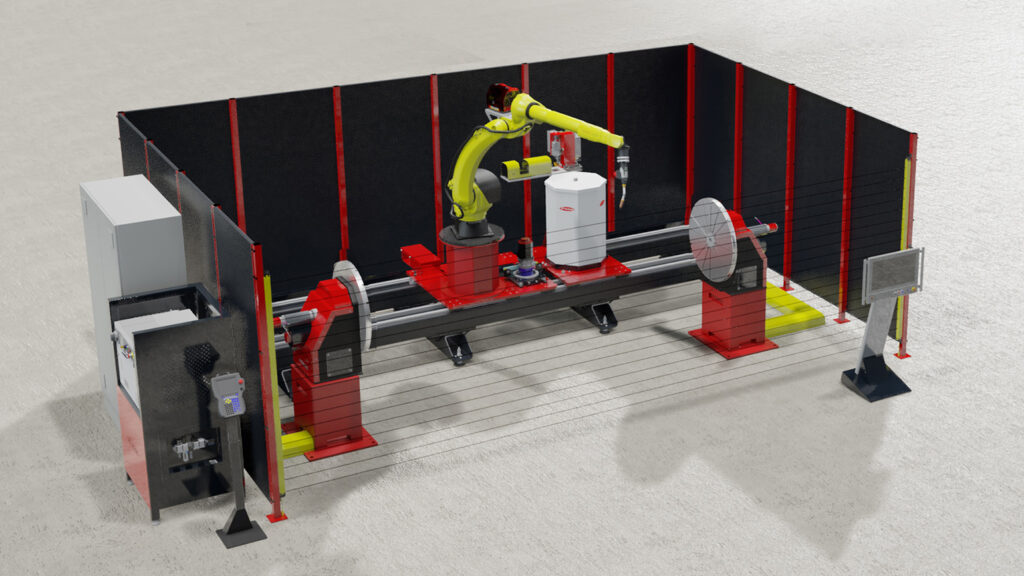
Zukunftsweisende Technologie
Fronius hat das Engineering von Roboterschweißzellen standardisiert und setzt dabei auf den Plattformgedanken. Einzelne Module mit spezifischen Aufgaben garantieren ein hohes Maß an Flexibilität bei Größe, Form und Gewicht von Bauteilen.
Schlichtweg genial: die Systemsteuerung HMI-T21 RS , aber auch die Offline-Programmier- und Simulations-Software Pathfinder®. Vor allem die HMI-T21 RS ist in puncto Funktionsumfang und Bedienkomfort wegweisend. Sie leitet eine völlig neue Generation der Systemsteuerungen ein. Pathfinder wiederum setzt neue Maßstäbe im Bereich der Offline-Programmierung und Schweißsimulation.
Keine Kommentare