An all-singing, all-dancing solution? In many areas of life, they still don’t exist yet. But is it true that there is now ONE universal solution in the field of welding systems? Is there one system to suit all applications? Is there ONE ideal process? Of course not. However, we are talking exclusively about the area of steel welding and the MAG process. One thing quickly becomes clear: where pulsing is used, many things become much easier, and this also applies to the welding of steel…
…
…
…
…
Pulsing? Yes of course it makes sense! But when and where should it be used?
Pulse welding offers a lot of advantages over other arc types, and this is also the case with the welding of steel. We described these advantages in detail in our article “MIG/MAG pulse welding – why do we use it?” The key finding from this article was that it makes particular sense to move over to pulsing in the intermediate arc range. This is because it is particularly in this range that increased welding spatters occur and the weld surfaces become unattractive. In some cases, this results in huge amounts of rework.
…
Pulsing? Yes of course it makes sense! But where is it not the best option?
In short, in the lower power range of the standard arc (dip transfer arc) and in the high-power range (spray arc). Pulse welding does bring with it reduced heat input, but the high current peaks of the pulse current can become a problem specifically in the field of ultra-light gage sheet welding. While the periods of high current are of course very short, they can still result in you burning through the sheet in ultra-light gage sheet welding, making pulsing counter-productive here.
Pulsing is also detrimental in the high-power range because the pinch effect that occurs here with the spray arc (pinching of droplets) generates a smooth material transfer. The material basically flows into the weld pool and the arc can be guided in an extremely soft way. Pulse welding would disrupt the flow and slow the welding speeds.
…
Nevertheless, the question remains, why is pulsing being used in all power ranges in steel welding?
It’s not quite that simple. If we look at day-to-day work in companies in the steel welding sector, one thing quickly becomes clear: irrespective of the power range, pulsing is an unremitting trend. The pulsed arc is now being used over a very large power range and often instead of the solid dip transfer arc and as an alternative to the soft spray arc.
It is therefore not only a question of avoiding the spattering intermediate arcs, or reducing the rework associated with these. Another logical reason for using pulsing is that, during their working day, welders do not just spend time welding in flat positions. In many cases, position welding is also taking place in various tight spaces—for example, fillet welds, butt welds, and much more.
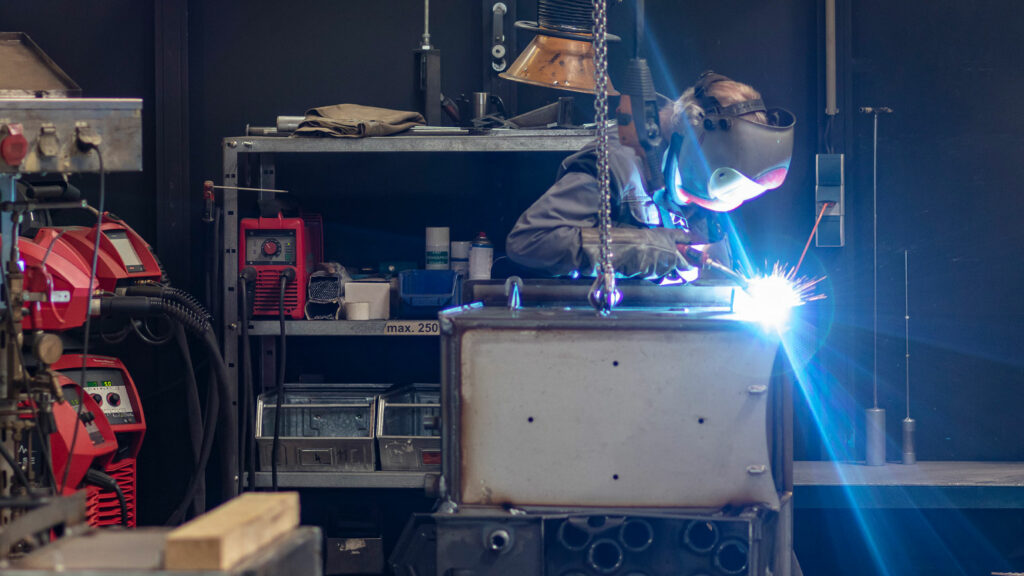
In these cases, pulse welding is the perfect alternative to arcs due to its heat reduction and slightly reduced penetration. Time-consuming oscillation and other special techniques for position welding can also largely be dispensed with. This in turn represents a time saving meaning that ultimately welding can be carried out more quickly.
…
Pulsing is simply better!
In addition, skilled workers describe pulsing in the welding of steel as “the better way to weld.” And probably the most decisive aspect here is the fact that if welders use the pulsed arc in a standard way, they hardly ever need to redefine the parameters on the welding system. Only the power is adjusted depending on the welding task to be carried out. This makes the handling of the welding system much easier as a large portion of the power range can be covered with just one arc.
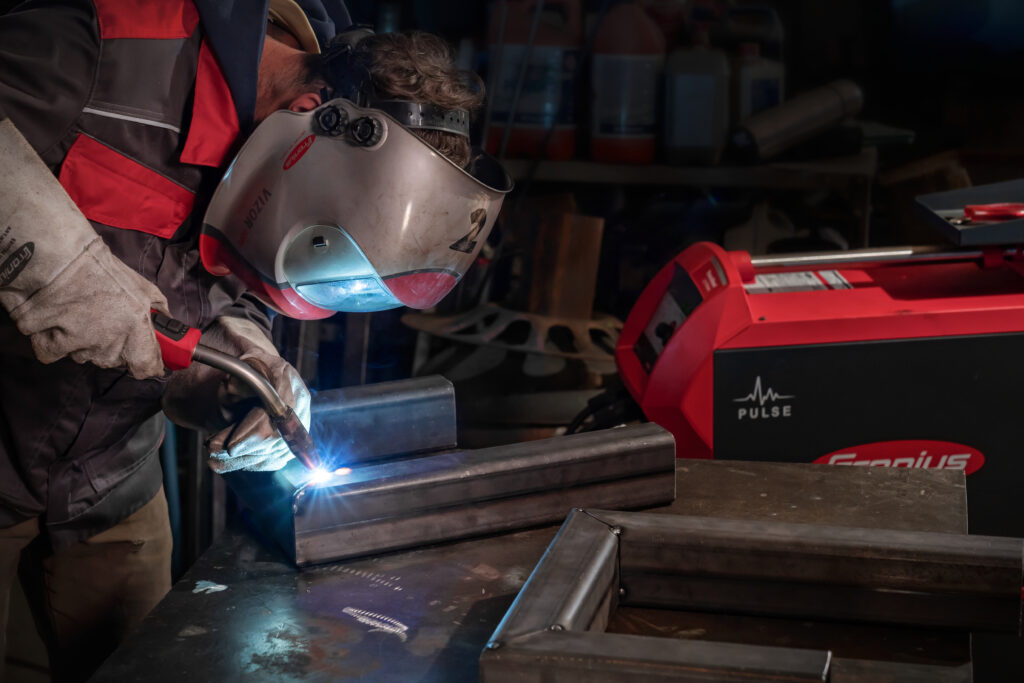
The background noise during pulsing is actually the same across all power ranges and is thus more pleasant. Welders often say controlling the weld pool is better, more consistent and more even over the entire power range, and this could also have something to do with the feel-good factor of the background noise…
…
Pulse welding systems for manual welding are also available from Fronius
Have we sparked your interest in pulsing in the welding of steel? If so, we’re pleased that is the case because we have devoted a great deal of attention to this topic at Fronius. And that is why we have chosen to upgrade our product portfolio, specifically for the manual welding segment, through the addition of TransSteel Pulse. Since expanding the TransSteel series to include the pulse welding function, we have been experiencing significant demand. Further information on TransSteel Pulse can be found here.
2 Comments
Suyash
5. August 2022 at 11:05Thanks!
Really helpful article.
redakteur
9. August 2022 at 8:34Thank you very much!