Fahrsicherheitssysteme im Auto, und Roboterschweißen in der industriellen Produktion – gibt es hier Gemeinsamkeiten? Betrachtet man zunächst die Entwicklungsschritte des KFZs, waren es anfangs noch analoge Systeme wie die Servolenkung, welche das Fahren um Welten erleichtert haben. Nach und nach kamen immer mehr digitale Helfer im Bereich der passiven Sicherheit dazu, beispielsweise ABS, ESP, Spurhalteassistenten und viele mehr. Heutzutage stehen wir kurz vor dem selbstfahrenden Automobil …
Auch die Entwicklung des Roboterschweißens hin zur Autonomie ist ein wesentliches Anliegen in der industriellen Serienfertigung. Seit Jahrzehnten geht das Bestreben der großen Produktionen in diese Richtung. Ein wesentlicher Schlüssel dazu könnten digitale Assistenzsysteme für das Roboterschweißen sein, die auf den Schweißgeräten installiert sind. Mit ihrer Hilfe agieren Roboter immer selbstständiger, ohne allzu große Eingriffe von außen.
Teachen des Schweißroboters leicht gemacht
Die Grundvoraussetzung jeder soliden vollautomatisierten Schweißung ist eine genaue Programmierung des Schweißroboters. Der Schweißer muss dem Roboter also beibringen, wo genau sich der Schweißnahtverlauf im dreidimensionalen Koordinatensystem befindet, auf welchem die Robotersteuerung basiert.
Professionelle Assistenzsysteme für das Roboterschweißen legen hierfür zum Beispiel eine geringe Sensorspannung an den Draht an. Steuert der Schweißer nun den Roboterbrenner zum Bauteil auf die definierten Start- und Endpunkte der Schweißung, gibt es bei der Blechberührung einen Kurzschluss – aufgrund der geringen Spannung jedoch ohne Schweißung. Dieser Kurzschluss wird von der Stromquelle in ein digitales Signal umgewandelt, welches wiederum dem Roboter zur Verfügung gestellt wird. Kommt ein Signal rein, kann er seine Positionsdaten speichern – Start- und Endpunkte der Schweißnaht sind somit exakt registriert.
Die Berührung des Werkstücks birgt jedoch Risiken. Bei herkömmlichen Brennern, inklusive ihrer Standart-Drahtfördersysteme, besteht eine hohe Wahrscheinlichkeit den Draht zu verbiegen. Hier leisten Systeme mit reversibler Drahtförderung – also einer Vor-Zurückbewegung des Drahtes – Abhilfe. Im Moment der Blechberührung wird der Draht automatisch zurückgezogen, eine Beschädigung der Drahtelektrode – und dadurch verfälschte Positionsergebnisse sind somit ausgeschlossen.
Die Drahtelektrode als Sensor
Sensorspannung am Schweißdraht in Kombination mit einer reversierenden Drahtförderung lässt es bereits erahnen: Hier sollte noch viel mehr möglich sein! Die leistungsfähigsten Systeme machen mittlerweile Draht-Vor-Zurück-Bewegungen mit bis zu 100 hz möglich. Würde man den Schweißdraht unter dieser hochdynamischen Bewegung in endlos aneinandergereihten Bahnen über das Bauteil tasten lassen, könnte jede Hebung und Senkung am Bauteil registriert werden. Prinzipiell ließen sich somit komplette Konturen in 3D sichtbar machen.
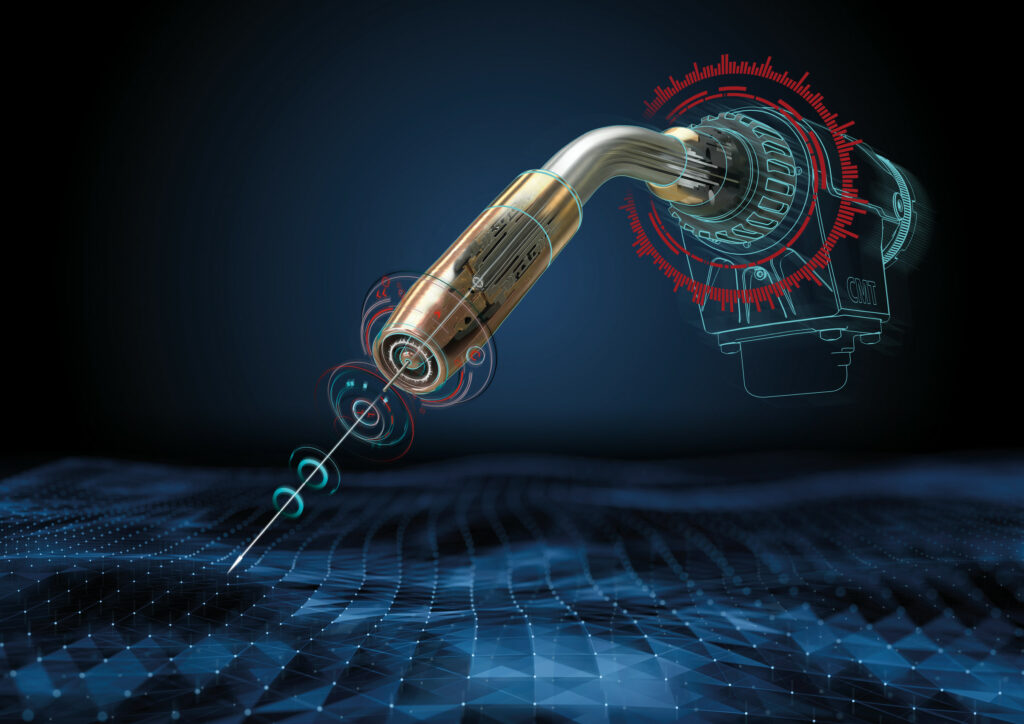
Kantendetektion: Korrigieren der Roboterbahn
In der Praxis lässt sich diese neugewonnene Sensorik der Drahtelektrode bereits jetzt höchsterfolgreich einsetzen. Die Kantendetektion bei Überlappnähten ist dabei eine der wichtigsten Ausprägungen, die in der industriellen Produktion mittlerweile umgesetzt werden. Aufgrund automatisierter Systeme, welche die Unter- und Oberbleche für die Schweißung in Position bringen, kommt es immer wieder zu Abweichungen – man spricht hier auch von Toleranzen. Weicht die Position der Kante des Oberblechs nun von den programmierten Sollwerten zu stark ab, entstehen infolge Bindefehler bei der Schweißung.
Eine Suchfahrt im Vorfeld der Schweißung auf festgelegten Bahnen registriert genauestens, um wie weit die IST-Werte der Blechkannte von den SOLL-Werten abweichen. Der Schweißnaht-Verlauf kann somit von der Robotersteuerung selbstständig entsprechend korrigiert werden und eine perfekte Anbindung von Unter- und Oberblech ist das Ergebnis.
Höhenmessung: Zuverlässige Schweißung trotz Spalt
Doch die Blechpositionen der Bauteile verschieben sich nicht nur horizontal. Natürlich können sich auch unbeabsichtigte Höhenunterschiede zwischen Unter- und Oberblech ergeben. Auch diese führen bei zu großen Spaltmaßen in der Regel zu Bindefehlern.
Da mit dem digitalen Signal auch die exakt vermessene Blechkantenhöhe übermittelt wird, ist man mit dem Schweißdrahtsensor in der Lage, Spalte zwischen den Blechen exakt zu errechnen. Darüber hinaus kann im Vorfeld genau festgelegt werden, wie die Stromquelle auf die unterschiedlichen Spaltmaße reagieren soll: Je nach Spaltgröße greift sie hierfür automatisch auf diverse hinterlegte Schweißprogramme zurück – sogenannte Jobs. Infolge wird die jeweilige Schweißherausforderung also mit genau den Schweißparametern ausgeführt, die dem Spaltmaß ideal angepasst sind.
Nahtverfolgung und -korrektur während des Schweißens
Die bisher genannten Möglichkeiten der Sensorik sollen allesamt den Positionsabweichungen der Bleche im Vorfeld der Schweißung entgegenwirken. Doch was tun, wenn sich während des Schweißvorgangs gröbere Abweichungen ergeben? Gerade im Dickblechbereich, etwa bei der Fertigung von Schienen- oder Baufahrzeugen, kann es durch die massive Wärmeeinbringung zu geometrischem Verzug kommen, auf den es im Moment der Schweißung zu reagieren gilt.
Muss zum Beispiel eine Kehlnaht oder angearbeitete Stumpfnaht geschweißt werden, führt der Roboter die Schweißung in einer Pendelbewegung aus. Dabei verändert sich stetig die Stickout-Position von einer zur anderen Seite. Damit einhergehend ändern sich natürlich auch die einzelnen Schweißparameter, wie Spannung und Stromstärke. Weicht nun eines der beiden Bleche aufgrund der Hitzeeinwirkung von seiner Position ab, spiegeln das die Unterschiede in Soll- und Istwerten der Schweißparameter wieder.
Der Schweißroboter kann aufgrund dieser Informationen automatisch den Schweißnahtverlauf während der Schweißung korrigieren. Bindefehler werden somit wiederum äußerst unwahrscheinlich.
Kostenersparnis durch Assistenzsysteme für das Roboterschweißen
Roboterschweißen soll Stück für Stück in die autonome Produktion geführt werden. In Summe ermöglichen die dafür verwendeten Assistenzsysteme effizientere und zuverlässigere Abläufe. Die Nacharbeit an Bauteilen, sonstiger Arbeitsaufwand sowie Materialkosten können dadurch erheblich verringert werden. Die Produktionskosten insgesamt werden dadurch bestmöglich reduziert.
Fronius ist mittlerweile auch bei Assistenzsystemen für das Roboterschweißen Vorreiter sowie Technologieführer. Mit zahlreichen Entwicklungen, wie zum Beispiel dem 2020 gelaunchten System WireSense, gelingt es Fronius die vollautomatisierte Produktion mittels Schweißrobotern erfolgreich voran zu treiben. Somit ist die Stromquelle nicht mehr nur Schweißgerät, sondern wird gleichzeitig intelligentes Gehirn des Roboters.
Keine Kommentare