Was hat eines der geländegängigsten und dabei alltagstauglichsten Fahrzeuge weltweit mit der Dokumentation von Schweißdaten zu tun? Eines lassen die enorme Bodenfreiheit sowie riesige Wattiefe des Mercedes G sofort erahnen: Das Fahrzeug muss härtesten Offroad-Bedingungen standhalten können – Zugkraft und Langlebigkeit müssen dabei immer gewährleistet sein. Wenn der G heftigen Stößen bei hoher Geschwindigkeit in unwegsamem Gelände ausgesetzt ist, bedeutet das auch eine unentwegt hohe Belastung für sämtliche Schweißnähte. Deshalb sind die Qualitätssicherung und Optimierung der Produktionsabläufe auf der Basis eines ausgereiften Schweißdatenmanagement-Systems hier so entscheidend.
Rahmenproduktion des Mercedes G bei Magna Presstec
Die höchsten Qualitätsansprüche an die G-Klasse – gefordert von Herstellern sowie Endverbrauchern – spiegeln sich auch in der Nachfrage wider: Das Interesse am Luxus-Offroader steigt unablässig. Um den geforderten Stückzahlen nachkommen zu können, ist in der Produktion des Fahrwerksrahmens ein hoher Automatisierungsgrad zwingend notwendig.
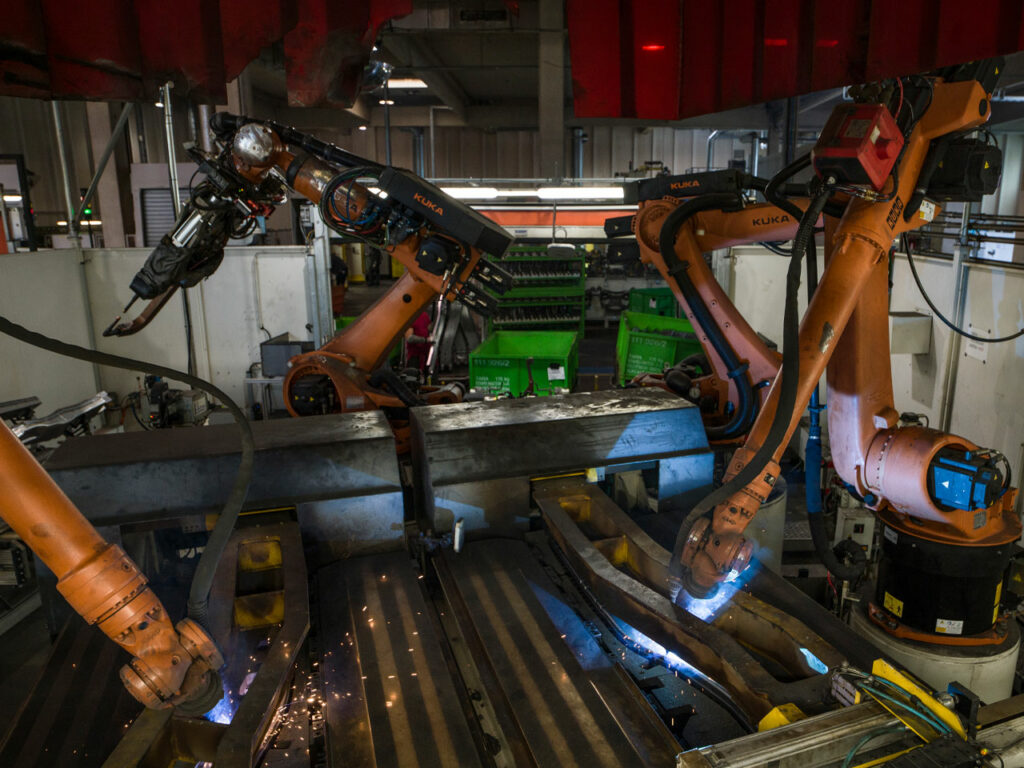
Die Hightech-Fertigungslinie des Tier-1-Zulieferers Magna Presstec in Lebring, im Süden Österreichs, hat es in sich: Auf einer Länge von 100 Metern greifen Schweiß- und Handling-Robotersysteme perfekt ineinander. Ein extrem schneller, hochpräziser und digital gesteuerter Puls-Schweißprozess (PMC von Fronius) erfüllt dabei die hohen Ansprüche hinsichtlich der grundlegend notwendigen Fügetechnik.
Lediglich zu Beginn wird die Produktionsanlage mit Einzelteilen bestückt. Alle 10 Minuten verlässt dann ein fixfertiger Mercedes-G-Fahrwerksrahmen – wie von Zauberhand am Deckenkran aufgehängt – die Werkhalle.
Überaus komplex: autonome Spitzenproduktion im Detail
„Unser Anspruch ist, dass jeder Rahmen absolut gleich ist. Abweichungen gilt es auszuschließen“, erklärt Kurt Hartmann, Produktionsleiter und Schweißaufsicht bei Magna Presstec, nachdrücklich.
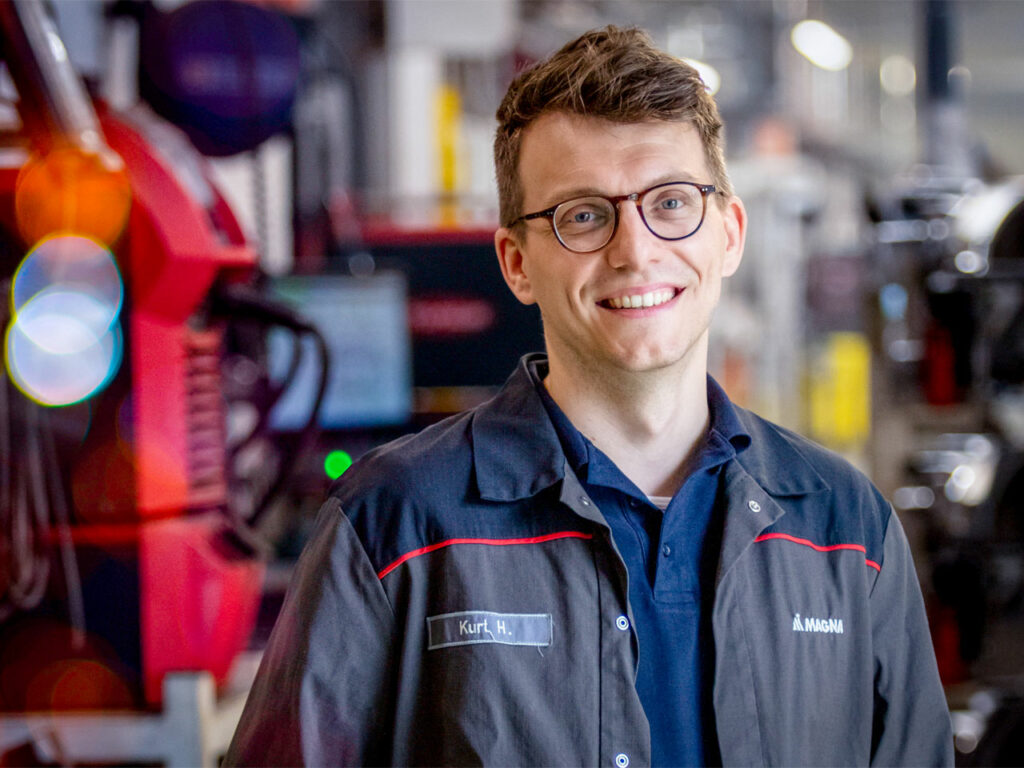
Vorder- und Hinterbau: „Wir fertigen hier in drei Abschnitten“, geht Hartmann ins Detail. „Vorderbau und Hinterbau (des Rahmens) – also die ersten beiden Abschnitte der Produktionsanlage – werden simultan produziert. Hier bestücken zu Beginn einige Mitarbeiter die Schweißvorrichtungen.
In den Zellen werden die Komponenten dann mittels Schweißrobotern gefügt. Ein Handling-Roboter nimmt die fertigen Komponenten auf, transportiert sie zur nächsten Zelle und bringt sie in Position. Am Ende jedes Abschnitts gibt es eine Zelle, die für die Mitarbeiter unzugänglich ist. Diese dient dem Ausschweißen der langen Nähte. Die Zellen werden aber auch als Abkühlstation verwendet oder als komplexe Station, wie zum Beispiel für das Squeezing: Hier werden die Unterschalen mit den Oberschalen der Längsträger verschachtelt, in Position gebracht und unter Druck verschweißt.“
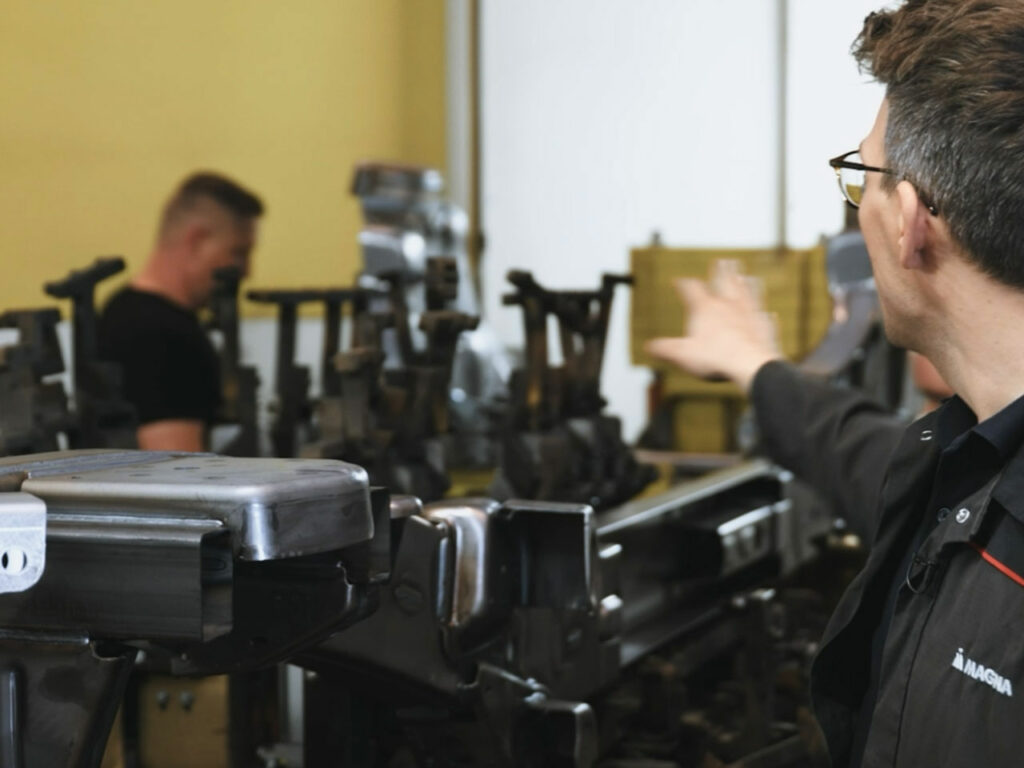
Unterbau: „Im Unterbau – dem letzten Fertigungsabschnitt – werden Vorder- und Hinterbau miteinander verheiratet. Der Rahmen nimmt seine markante Form an“, führt Hartmann weiter aus. Die letzten Arbeitsschritte beinhalten dann das Stanzen von ausgekoppelten Anbindungspunkten für das Fahrwerk. Zusätzlich werden mittels Hubzündung 192 Bolzen auf den Rahmen geschossen. Ein geschulter Nachschweißer kontrolliert anschließend die Qualität der Schweißnähte, entfernt letzte Schweißspritzer und arbeitet gegebenenfalls Nähte nach.
Zur vollständigen Qualitätssicherung folgt noch eine hundertprozentige Vermessung des Rahmens mittels robotergesteuerter Lasermesstechnik. Nachdem der Rahmen das letzte Mal kontrolliert wurde, verlässt er über eine Power&Free-Anlage (Förderbahn) den Rohbau. Es erfolgt die Übergabe an weiterführende Prozessschritte.
Zur Qualitätssicherung: Überwachung der Schweißdaten mittels WeldCube Premium
Doch ein hervorragender Schweißprozess alleine reicht nicht aus, damit Magna Presstec die enormen Qualitätsansprüche des G-Modells bedienen kann. Benötigt wird ein System, das die fehlenden „Augen“ auf den 100 Metern Produktionslänge ersetzt – also die Möglichkeit einer 100%igen Überwachung und lückenlosen Dokumentation des Schweißprozesses.
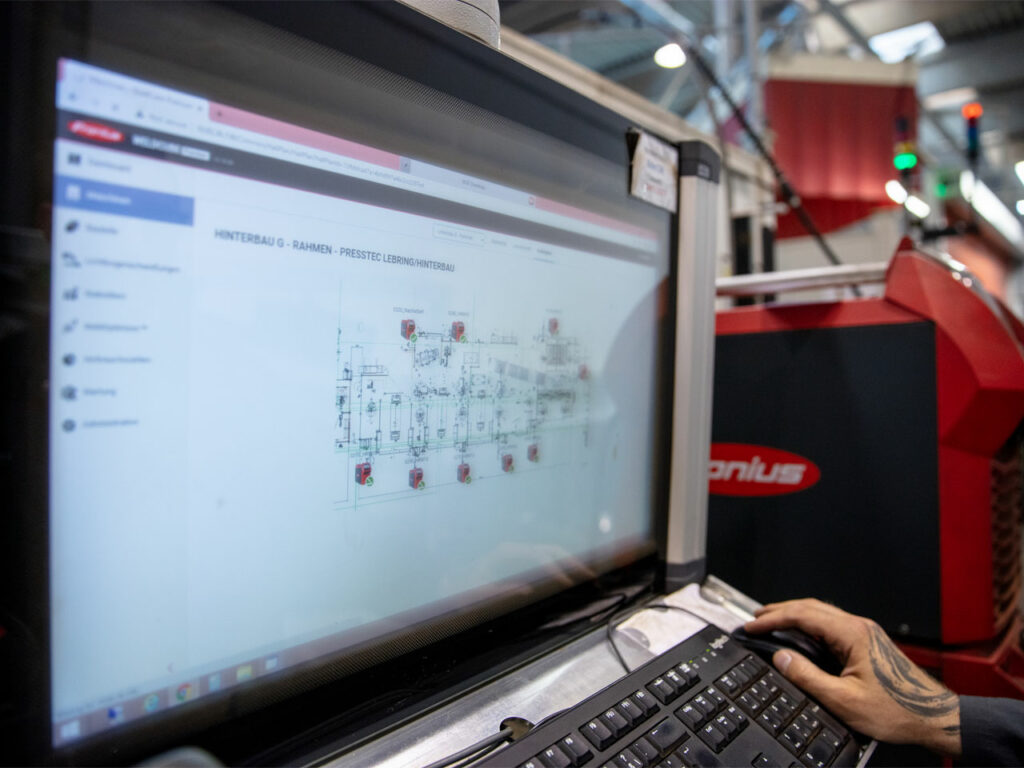
„In der Produktionshalle ist die Software WeldCube Premium ein wesentlicher Pfeiler unseres Qualitätsmanagements“, zeigt sich Hartmann überzeugt. „Die absolute Nachverfolgbarkeit jeder einzelnen Schweißnaht ist für uns immanent wichtig. An den Qualitätskontrollplätzen bekommen die geschulten Mitarbeiter via Terminal genaueste Informationen aufbereitet: Gibt es auffällige oder tatsächlich fehlerhafte Nähte?
Durch WeldCube – also anhand der Schweißdaten – werden mögliche Fehlerstellen aufgezeigt, einer detaillierten Sichtprobe unterzogen und gegebenenfalls nachgearbeitet. Erst dann wird der G-Rahmen für weitere Prozessschritte freigegeben.“ Die gesammelten Daten fließen wieder in die Optimierung der automatisierten Schweißprozesse ein.
Vom Monitoring bis zur vorausschauenden Wartung
„Da WeldCube Premium jeden Millimeter Schweißnaht ausnahmslos aufzeichnet, können wir mittels der Analysetools spielerisch die Kosten für Verbrauchsmaterialien wie Gas und Schweißdraht berechnen. Doch wir sehen hier noch deutlich mehr Potential: Ein Punkt wäre sicherlich Predictive Maintenance (vorausschauende Wartung) – respektive die Möglichkeit, rechtzeitig und in ausreichender Menge Verschleißteile und Werkstoffe zu ordern“, skizziert Hartmann naheliegende Zukunftsaussichten.
„Predictive Maintenance mittels WeldCube Premium könnte uns zusätzlich enormes Sparpotential bieten – zum Beispiel, wenn uns das Schweißdatenmanagement genaue Wartungsintervalle vorgibt. Über den Zustand von Kontaktrohren, Rohrbögen, Brennern und Vorschubgeräten wüssten wir also immer genauestens Bescheid. Somit könnten wir die Geräte zur richtigen Zeit servicieren, wodurch wiederum fehlerhafte Schweißnähte, Nacharbeit oder gar Bauteilausschuss vermieden werden.“
Für spezielle Aufgaben: nur Spezialisten!
Doch die Dokumentation und Analyse von Schweißdaten reicht Magna Presstec nicht aus: „Darüber hinaus verwenden wir bereits jetzt die Softwarelösung Central User Management (CENTRUM) – die uns ebenfalls im Qualitätsmanagement unterstützt. Damit vergeben wir zentralgesteuert Benutzer- und Schweißberechtigungen. Die Schweißer müssen sich dann mittels Chipkarte am Schweißgerät authentifizieren. Dadurch können wir sichergehen, dass nur für spezifische Aufgaben geschulte Mitarbeiter am richtigen Platz mit den dafür vorgesehenen Parametern arbeiten. Weitere Fehlerquellen schließen wir somit bestmöglich aus“, ist Hartmann überzeugt.
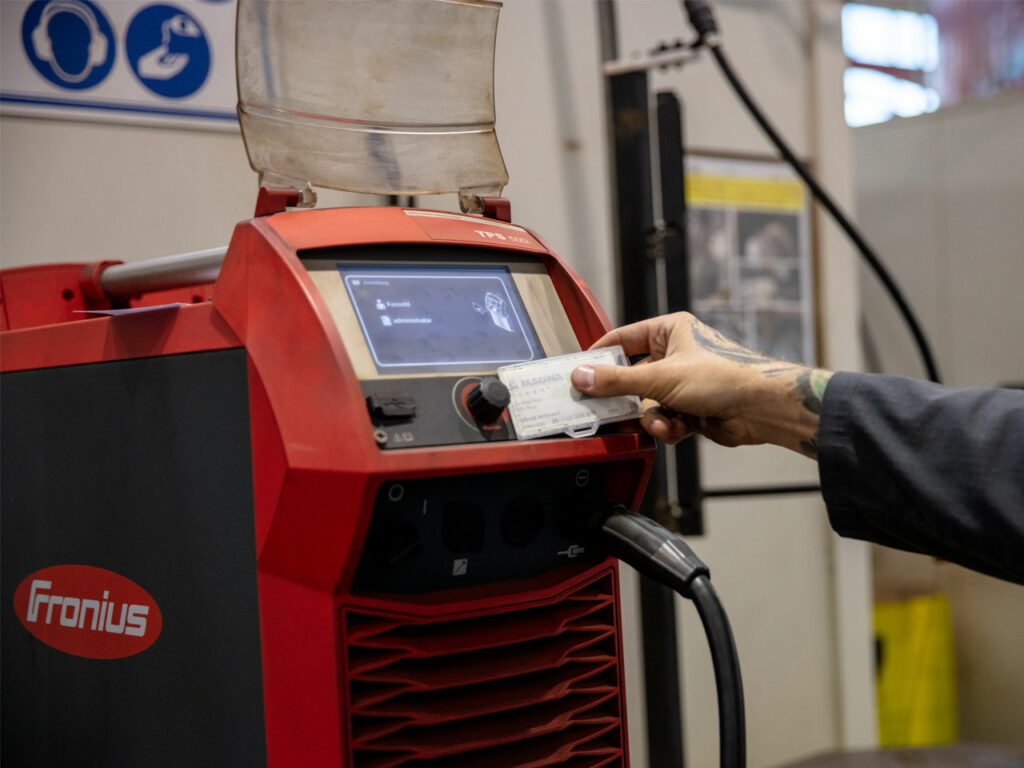
Lösungen rund um die Dokumentation von Schweißdaten bei Fronius
Die von Magna Presstec angewendeten Softwarelösungen sind allesamt von Fronius entwickelt worden. Angefangen mit WeldCube Premium bis hin zu Central User Management sind jedoch alle Produkte im intensiven Austausch mit Magna Presstec entstanden: Erst durch das Langzeit-Testing von Prototypen in der Magna-Produktion konnten notwendige Informationen gewonnen und die Marktreife erreicht werden.
Schauen Sie sich gleich mal unsere Kurzdoku zur Rahmenproduktion des Mercedes G beim Tier-1-Zulieferer Magna Presstec an:
Falls Sie ebenfalls Interesse an unseren zukunftsorientierten Lösungen zur Unterstützung autonomer Produktion haben, stellen wir Ihnen hier weitere Produktinformationen zur Verfügung.
Keine Kommentare