Stunde für Stunde, fünf Tage in der Woche: Wer professionell MIG/MAG-schweißt, kann gar nicht anders, als den Schweißbrenner in- und auswendig zu kennen. Doch was macht einen guten Schweißbrenner eigentlich aus? Und ist das, was Schweißfachkräfte in ihrem Berufsalltag regelmäßig in der Hand halten, tatsächlich die beste aller Lösungen? Mit diesen und ähnlichen Fragen beschäftigen sich die Entwicklerinnen und Entwickler von Schweißbrennern. Wir haben ihnen über die Schulter geschaut und erklären, wie neue Schweißbrenner entstehen und wieso der „Faktor Mensch“ so eine tragende Rolle spielt.
Vorne am Schweißbrenner treffen nicht nur das Schweißgerät, der Lichtbogen und das Werkstück aufeinander. Der Griff des Brenners ist auch das Bindeglied zwischen Mensch und Maschine – und damit der verlängerte Arm von Anwenderinnen und Anwendern.
Doch was erwarten sich Schweißerinnen und Schweißer von einem neuen Schweißbrenner überhaupt? Eine grundlegende Antwort vorweg: Bei manuellen Schweißbrennern geht es nicht ausschließlich um gut funktionierende Technik, hervorragende Schweißleistungen und hohe Standzeiten bei den Verschleißteilen.
Mindestens ebenso wichtig sind Nutzerfreundlichkeit, Ergonomie und Emotionen, also wie gut ein Schweißbrenner in der Hand liegt, wie einfach sich Einstellungen darauf vornehmen lassen – und nicht zuletzt, wie „sympathisch“ der neue Schweißbrenner insgesamt bei Schweißerinnen und Schweißern rüberkommt.
Regionale Unterschiede bei Schweißbrennern
Ein Blick um den Globus macht hier durchaus Unterschiede deutlich: Während im asiatischen Raum eher kleinere und leichte Schweißbrenner bevorzugt werden, setzen viele Schweißer in den USA auf sehr massiv gebaute und wuchtig aussehende Brenner. Europa liegt bei der Größe der Schweißbrenner im Mittelfeld – wobei „europäische Standards“ auch global immer mehr an Bedeutung gewinnen.
Neuentwicklung von Schweißbrennern: Wer gibt den Anstoß?
Schweißbrenner gibt es seit mehr als hundert Jahren – und dennoch kommen Jahr für Jahr neue Brennertypen auf den Markt. Für Neuentwicklungen gibt es vier wesentliche Gründe:
1) Weil es der Kunde so will
Der wohl wichtigste Grund für Innovationen bei Schweißbrennern sind geänderte Kundenanforderungen: Unternehmen, die vor neuen Herausforderungen stehen, treten an die Brenner-Hersteller heran und verlangen nach entsprechenden Lösungen. Beispielsweise, um mit einem neuen Schweißbrenner schwierig zu erreichende Stellen mit einem neuartigen Verfahren zu schweißen.
2) Neues Schweißgerät + neuer Schweißbrenner = perfektes Schweißsystem
Wesentliche Anstöße zu Neuentwicklungen kommen aber auch aus den Schweißtechnik-Unternehmen: Wird eine neue Schweißgeräte-Serie auf den Markt gebracht, werden in der Regel auch neue Brennertypen entwickelt, die optimal auf die Technologie der neuen Geräte abgestimmt sind. Nur wenn alle Bereiche des Systems – vom Schweißbrenner bis zum Gerät – perfekt miteinander interagieren, können Schweißende maximal von technischen Innovationen profitieren.
3) Ideen aus den Forschungs- und Entwicklungsabteilungen
Für gute Ideen braucht es nicht immer einen konkreten Anlass: Bei Schweißbrennern entstehen technische Innovationen immer wieder dadurch, dass Entwicklungsingenieurinnen und -ingenieure ihre „kreativen Freiräume“ nutzen und dabei Neues entdecken.
4) „Normative Anforderungen“ an Schweißbrenner: Weil es das Gesetz will
Ein nicht zu ignorierender Anstoß für Innovationen bei Schweißbrennern sind nicht zuletzt geänderte „normative Anforderungen“ – also Änderungen bei den gesetzlichen Bestimmungen. Ein sehr augenscheinliches Beispiel dafür: Die Entwicklung von Schweißbrennern mit Absaug-Einrichtung, nachdem auf EU-Ebene die Arbeitsschutz-Bestimmungen für Schweißfachkräfte verbessert wurden – und sich dadurch Brenner ohne entsprechende Absaugung gebietsweise nur noch schwer verkaufen lassen.
Schweißfachkräfte entscheiden, ob sich ein Schweißbrenner verkauft
Bei wenigen anderen Teilen eines Schweißsystems kommt es so sehr auf den „Faktor Mensch“ an wie beim Brenner. Letzten Endes entscheiden die Anwenderinnen und Anwender, ob ein neu entwickelter Schweißbrenner zum Verkaufserfolg wird – oder zum Ladenhüter: Einfach, indem sie die Vorteile eines neuen Brenners erkennen und ihn in ihrer täglichen Arbeit einsetzen – oder indem sie doch lieber bei ihrem alten Brenner-Modell bleiben, an das sie gewöhnt sind und das ihnen jahrelang gute Dienste geleistet hat.
So wird ein Schweißbrenner entwickelt: 5 Schritte
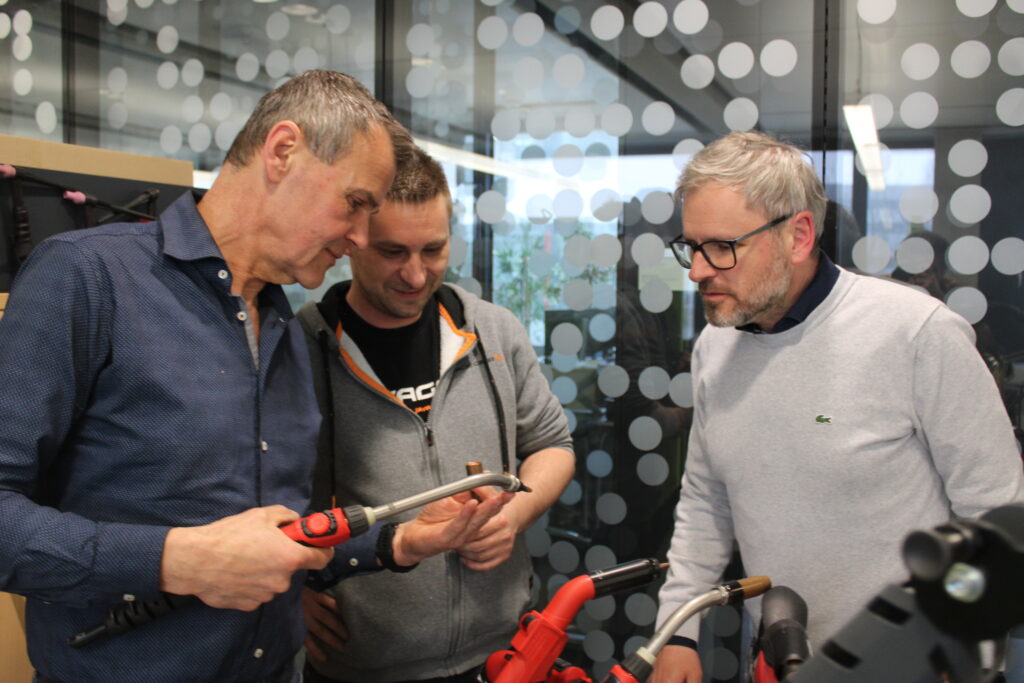
Auf welche Art und Weise Schweißbrenner entwickelt werden, hängt natürlich vom jeweiligen Unternehmen ab. Stark vereinfacht lässt sich der Entwicklungsprozess in folgenden Schritten zusammenfassen:
Schritt 1: Konzeptphase
Zu Beginn werden alle Anforderungen, die der neue Schweißbrenner erfüllen soll, in einem Lastenheft zusammengefasst. Und dann geht es auch schon los: Die Technikerinnen und Techniker in den Entwicklungsabteilungen setzen sich vor ihre PCs und beginnen mit der Konstruktion.
In gut ausgestatteten Schweißtechnik-Unternehmen werden vorab rein digitale 3D-Modelle des neuen Brenners entworfen. Diese „virtuellen Schweißbrenner“ unterlaufen dann in Simulatoren – also speziell dafür ausgestatteten Hochleistungsrechnern – umfangreiche Tests. Mit solchen virtuellen Versuchen lassen sich die meisten Vorgänge, wie sie auch in „realen Schweißbrennern“ vorkommen, wirklichkeitsgetreu darstellen. Es gibt thermische, hydraulische und auch strömungstechnische Simulationen.
Schritt 2: Prototypen – der erste Realitätscheck
Kann am Simulator nichts mehr verbessert werden, wird es endlich „real“: Die ersten Prototypen entstehen. Diese sehen von außen meist noch etwas „zusammengebastelt“ aus, sollten aber bereits alle technischen Anforderungen erfüllen, die an den neuen Schweißbrenner gestellt werden.
Ob das tatsächlich so ist, wird abermals in umfassenden Tests festgestellt: Ein Lichtbogentechniker oder eine Lichtbogentechnikerin überprüft die Lichtbogenqualität und die Qualität der Schweißprozesse. Mithilfe von Wärmebildkameras und Temperatursensoren lässt sich die Temperaturverteilung aufzeichnen und optimieren, die Gasströme am Brenner können mittels Schlierenoptik dargestellt werden. Dies hilft unter anderem, die Schweißqualität zu verbessern und die Standzeiten von Strom- und Gasdüsen möglichst lange zu halten.
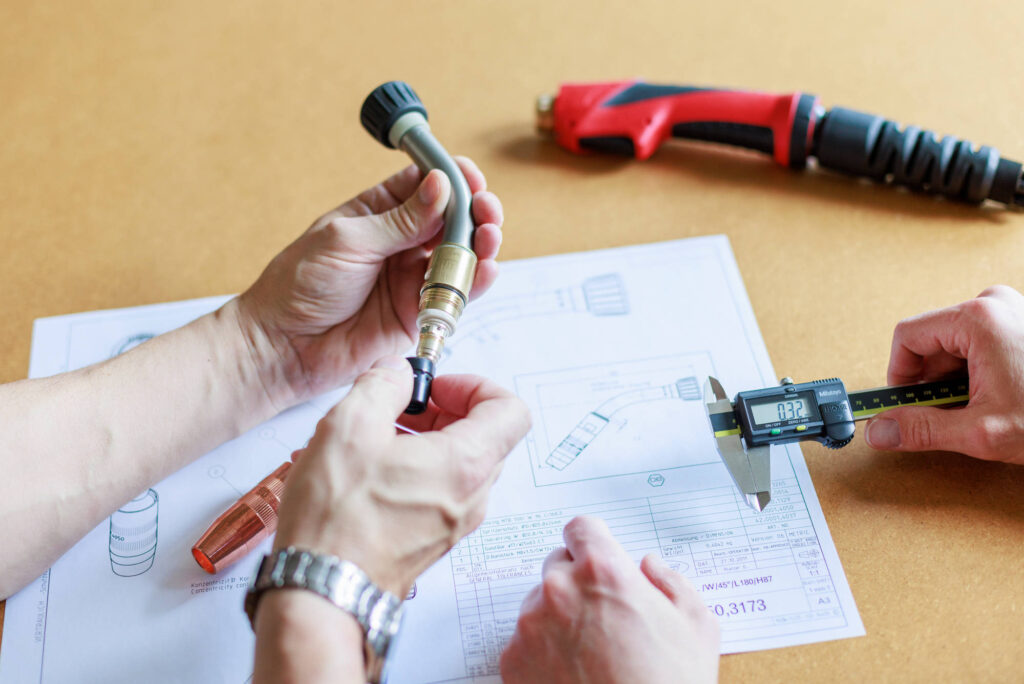
Schritt 3: Pflichtenheft und Vorserie
Nach den Prototypentests erstellt das Projektteam dann meist das Pflichtenheft. Darin sind alle Eigenschaften des neuen Schweißbrenners festgelegt– die Detailentwicklung kann starten. Parallel dazu werden die Werkzeuge für die Serienfertigung gebaut und Fertigungsprozesse definiert.
Vorserien gibt es auch bei Schweißbrennern unter anderem deshalb, damit diese auf „Herz und Nieren“ geprüft werden können, und zwar sowohl inner- als auch außerhalb des Unternehmens: Während bei den Herstellern umfassende Funktions- und Belastungstests stattfinden, werden Vorserien-Schweißbrenner häufig an ausgewählte Kunden geschickt. Diese setzen sie in der betrieblichen Praxis ein.
Schritt 4: Entscheidendes Kunden-Feedback zum Schweißbrenner
Die Rückmeldung der Kunden ist für die Schweißbrenner-Hersteller nicht zuletzt in Zusammenhang mit der Nutzerfreundlichkeit und Ergonomie ihrer Geräte von zentraler Bedeutung. Mitunter werden die Meinungen von Schweißerinnen und Schweißer zu einem neuen Brenner-Modell auch mittels Fragebogen eingeholt.
Schritt 5: Design-Freeze – die Produktionstechnikerinnen und -techniker übernehmen
Bisweilen sind mehrere Feedbackschleifen aus verschiedenen Unternehmensabteilungen und von maßgeblichen Kunden notwendig, bis ein Produkt perfekt ist. Kann der Schweißbrenner in den Augen seiner Entwicklerinnen und Entwickler nicht mehr weiter verbessert werden, kommt es zum Design-Freeze. Der Produktentwicklungsprozess ist damit abgeschlossen – die Produktionstechnikerinnen und -techniker übernehmen und richten die Serienfertigung ein.
Die hier genannten Punkte sind natürlich nur ein grober Abriss von dem, was bei der Entwicklung eines neuen Schweißbrenners vor sich geht. Wer mehr über die Produktentwicklungsprozesse bei Schweißsystemen erfahren möchte, findet Informationen darüber auch im Artikel „Vom WIG-Schweißgerät zum Multiprozess-System: Die Entwicklung der neuen iWave in 10 Schritten“.
Fazit: Beim Schweißbrenner kommt es auf die Schweißfachkräfte an
„Im Zentrum jeder Schweißbrenner-Entwicklung bei Fronius stehen die Schweißerinnen und Schweißer. Ihre Vorstellungen und Wünsche haben einen zentralen Einfluss auf unseren gesamten Entwicklungsprozess“, erklärt dazu Manfred Hubinger, technischer Produktmanager für Schweißbrenner bei Fronius.
„Gute Brenner-Entwicklerinnen und -Entwickler achten stets darauf, dass sich Schweißfachkräfte wohl fühlen. Neben modernster Technologie und Verlässlichkeit sind es vor allem Eigenschaften wie Nutzerfreundlichkeit und die richtige Ergonomie, die einen hervorragenden manuellen Schweißbrenner ausmachen. Er muss sich einfach bedienen lassen – und er muss gut in der Hand liegen“, so Christian Aitzetmüller, Produktmanager für Schweißbrenner bei Fronius abschließend.
Unser Artikel hat Ihr Interesse geweckt und Sie möchten mehr über Fronius Schweißbrenner erfahren? Dann schauen Sie gleich mal auf unserer Website vorbei! Dort finden Sie alle technischen Details und Informationen darüber, was Sie für Ihre jeweilige Anforderung brauchen.
Keine Kommentare